Search:
#
-
Ausrichtung aller Tätigkeiten auf den Kunden (Kundenorientierung)
-
Konzentration auf die eigenen Stärken
-
Optimierung von Geschäftsprozessen
-
Ständige Verbesserung der Qualität ( Kontinuierlicher Verbesserungsprozess , KVP)
-
Interne Kundenorientierung als Leitprinzip
-
Eigenverantwortung, Empowerment und Teamarbeit
-
Dezentrale, kundenorientierte Strukturen
-
Führen ist Service am Mitarbeiter
-
Offene Informations- und Feedback-Prozesse
-
Einstellungs- und Kulturwandel im Unternehmen.
(Quelle: nach Graf-Götz und Glatz Organisation gestalten, Beltz-Verlag)
dirty, dangerous, difficult (schmutzig, gefährlich, schwierig)
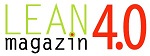
The three elements of just-in-time (JIT) are:
-
Cycle time
-
Flow manufacturing
-
The downstream pull system
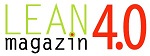
5S or also 5A (German-speaking area) is a workplace organization (methodology), which is used in production but also increasingly in the service sector. It is an idea from Japanese production concepts, which serves as an instrument to make workplaces and their surroundings safe, clean and clear. Without the basic prerequisite of cleanliness and order, neither quality work nor an improvement of work processes is possible. Objectives:
-
Trouble-free
-
No searching
-
Short transport routes
-
Avoidance of waiting times
ollows from this: => No waste As a methodical tool, the 5S can be applied in all areas of an organization 5S stands for:
-
Seiri: Sort out!
-
Seiton: Place properly!
-
So: Clean up!
-
Seiketsu: Keeping clean!
-
Shitsuke: Practice self-discipline!
However, some translations go to the A. This is why the concept is also known as 5A. 5A stands for:
-
Sort out!
-
Clean up! (Arrange work equipment ergonomically)
-
Workplace cleanliness!
-
Make arrangement the rule!
-
Keep to all points and improve!
Waste happens through:
-
Overproduction (too large quantity)
-
Stocks (too much material usage)
-
Transport (too long distances)
-
Waiting times (too much time)
-
Manufacturing process
-
Unnecessary movement
-
Occurring errors
Meanwhile 2 other types of waste are often discussed:
-
Waste through poor ergonomics (especially with regard to employees):
-
Not or wrongly used talent
The Failure Mode and Effects Analysis is actually a procedure for quality assurance of production and administration. Its formal principle is used in project management to translate uncertainties and risks into calculable processes. This is done with the help of tables, the first column heading of which often names the process to which a failure refers. The type, cause, probability of occurrence and consequences of the possible disruption/imponsibility are also listed in separate columns.
A
The ABC analysis is an easy-to-use method of situation analysis for setting priorities. It can be used to graphically illustrate concentration ratios (Lorenz curve). The original application was the determination of parameters in the distribution of income by the American Lorenz. In the materials management the ABC analysis determines the cost portion of the different camp parts of the camp total costs. In manufacturing the materials with the highest cost portion of the product interest the materials. In marketing and selling it applies to find the few articles which furnish together a high turnover portion of the total turnover.
(Source: GPM)
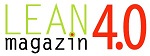
Recording the ("technological") conditions for the course of the project, determining deadlines and time limits, including their optimization and monitoring.
(Quelle: GPM)
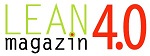
The process organization regulates the temporal and spatial order of the operational processes and procedures. It is supplemented by the Process organization.
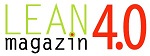
The ability to detect and rectify a fault, i.e. any deviation from a standard operation, in good time.
(Quelle: TBM Consulting Group http://www.tbmcg.com/de/about/ terminology.php)
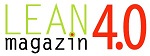
This team is entrusted with the solution of current individual problems and special tasks and works under a time limit. This term includes for example the execution team, the evaluation team and possibly also the project team.
(Quelle: Schneider: Lexikon zu Team und Teamarbeit)
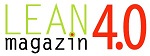
Evaluation of all change requests, especially if they affect project goals, initiation and monitoring of changes in the project result and its documentation
(Quelle: GPM)
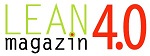
Acceptance refers to the more or less consensual attitude and attitude of an individual or a group towards an object, subject or other matter.
(Quelle: GPM)
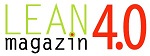
This term applies to a working group, whose members, separated from
hierarchy
to the rules and standards at their workplace. Individuality and independence are lost. The Alibi Team is not a real team, but a pseudo team.
(Quelle: Schneider: Lexikon zu Team und Teamarbeit)
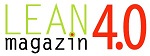
Die Fähigkeit sich mehrdeutigen und verwirrenden Anforderungen zu stellen oder auch mit einer unbekannten Situation fertig zu werden. Das Vermögen trotz größerer Unsicherheiten rationale Entscheidungen zu treffen.
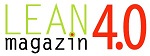
The analogy method belongs to the methods of Cost estimate. For this purpose, the project to be estimated is compared with similar, completed projects. An analysis of the deviations identifies similarities and differences between the projects with regard to the most important influencing factors (project organization, development environment, metrics, etc.). Afterwards an evaluation of these regarding effort and productivity takes place. The estimation accuracy depends on how well the project to be estimated is known (specification sheet) and on the experience in the correct selection and estimation of the influencing factors in the deviation analysis. Basis of the analogy method is extensive experience with similar, completed projects.
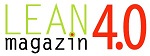
A visual signal. Usually this is a small light that has been attached to a machine and draws attention to possible problems or work stops.
(Quelle: TBM Consulting Group http://www.tbmcg.com/de/about/ terminology.php)
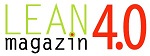
For connections of activities within a network it can happen that the start of an activity depends on the start of its predecessor. This dependency is called the initial sequence.
(Quelle: GPM)
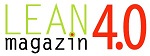
Definition nach DIN: Eine Anordnungsbeziehung ist eine quantifizierbare Abhängigkeit zwischen Ereignissen oder Vorgängen.
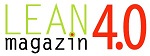
Trigger planning is a method of scheduling that is used in project management as phase planning for projects. Here the product to be created is divided into individual verifiable sections from its creation through its use to its disposal. This planning technique first roughly outlines the entire scope of the project, and then plans the nearest sub-sections step by step as finely as possible. In order to limit the technical and economic risk, the development of a product is divided into defined sections with fixed starting and end points. This step-by-step procedure allows a review of the work done and a forecast based on the experience gained and results at defined points in time. This planning process is typical for investment projects such as plant construction, factory construction and in the construction industry. The results of a completed phase are the basis for the next phase. This phase model also accommodates a way of thinking in budget units, but even so it sometimes endangers the overall project time due to missing approvals.
(Quelle: GPM)
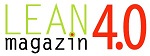
ASP - Application Service Provider Software is offered for rent over the Internet.
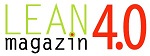
The correct work steps of an employee, executed in the correct order.
(Quelle: TBM Consulting Group http://www.tbmcg.com/de/about/ terminology.php)
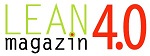
Definition according to DIN 69902: The work result is the quantity of units generated by the use and/or consumption of input materials.
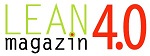
A work package (WP) is a part of the project that is not further subdivided in the work breakdown structure and can be on any level of structure (definition according to DIN). The work package should be defined as a self-contained element with clear boundaries and interfaces to other work packages so that it can be delegated to an organizational unit for processing. It forms the last and lowest element in a branch of the work breakdown structure. For further detailed planning, the work package can be broken down into individual tasks (activities). However, these activities are not listed in the work breakdown structure, but in detailed networks and Gantt charts. The sum of all work packages gives the complete picture of all the work that needs to be done to achieve the project goal.
(Quelle: GPM)
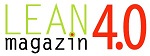
Time that is available within the standard work for a single work step.
(Quelle: TBM Consulting Group http://www.tbmcg.com/de/about/ terminology.php)
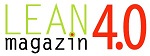
Application-Service-Provider-Software wird über das Internet zur Miete angeboten.
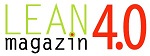
Die Aufbauorganisation dient der
-
Bildung von Stellen und Organisationseinheiten
-
Zuordnung der betrieblichen Aufgaben und Stellen
-
Zuordnung der Sachmitteln zu Stellen
-
Festlegung der Beziehungen zwischen den Stellen (Berichtswege und Informationsflüsse)
Die Organisation erfolgt nach Kriterien der Zweckmäßigkeit. Neben der klassischen funktionalen Stab-Linien-Organisation, werden heute mehr und mehr Prozeß- und Projektorganisationen gebildet. Das Begriffspaar Aufbauorganisation und Process organization prägt die deutsche Organisationslehre.
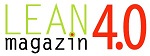
If the tasks in the area of investigation provide the decisive starting point for the project, a task breakdown is necessary. The analysis is carried out according to five structure points: Tasks, objects, rank, phase and purpose. The last three points are relevant to the content of each task and are therefore only formally listed. Which tasks are to be performed on which objects is of factual importance for the task analysis. The task classification is used when the tasks of a workplace or an area are to be systematically collected and presented in the context of an organizational project, and the tasks to be performed in the project are to be systematically recorded and planned. A task can be further executed according to the criteria object and performance in an AND-structure or an OR-structure. This enables a systematic recording of subtasks, which can be done according to the usual procedures of the as-is analysis (e.g. document analysis, interview, etc.). All tasks must be systematically arranged, complete and detailed. Instead of the map technique and the raster sheet method, the task analysis can also be supported by software programs. The individual tasks are arranged hierarchically and illustrated in an outline tree (structure picture). This technique can be used for all organizational questions of the project, but it only reflects the actual state and does not offer any solution approaches.
(Quelle: Mehrmann/Wirtz)
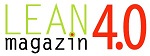
client needs are:
-
Timely provision of the agreed service
-
Full consideration of the client's needs and requirements
-
Kundenzufriedenheit
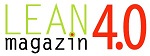
Contractor needs are:
-
Efficient handling of projects
-
Maintaining standards
-
Consideration of overarching aspects
-
Profitabilität
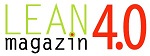
siehe Mengenproportionalität
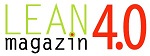
Determination of the time and resource requirements for all activities/work packages as the basis for the planning and control processes in the project.
(Quelle: GPM)
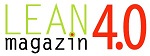
Cost estimation is the forecast of the personnel capacity requirements in a project. The quality of the effort estimation depends strongly on the underlying documents e.g. ACTUAL analysis, Specifications, Ausschreibungsunterlagen etc. ab. Die Aufwandsschätzung beruht auf 2 Größen Arbeitsmenge und Arbeitsproduktivität.
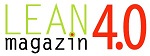
The expense value is a key figure in resource accounting. It describes the ratio of resource input to work result with the following formula:
Effort value = input resource cost/working result
(Quelle: GPM)
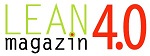
Expressive creativity is the lowest form of creativity. With this form of creativity, talent, know-how and originality of the thought presented are unimportant. Spontaneous drawings by children are typical examples. See also: emergent Creativity
, inventive-Creativity
, Iinnovative-creativity.
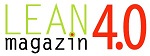
This special committee is usually entrusted by management with innovative tasks, for which a longer period of time is planned for implementation. Such an ad hoc committee is responsible for the implementation and monitoring of measures ordered by management (e.g. remediation committee, safety committee).
(Quelle: Schneider: Lexikon zu Team und Teamarbeit)
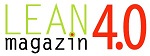
A plant in which all available capacities are precisely matched to demand.
(Quelle: TBM Consulting Group http://www.tbmcg.com/de/about/ terminology.php)
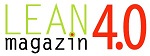
The time a machine takes to produce a unit, excluding loading and unloading.
(Quelle: TBM Consulting Group http://www.tbmcg.com/de/about/ terminology.php)
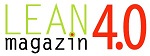
German equivalent of the Japanese word Jidoka. Stands for "human automation". A machine is equipped with human intelligence so that it stops automatically when a problem occurs.
(Quelle: TBM Consulting Group http://www.tbmcg.com/de/about/ terminology.php)
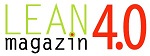
B
The Balanced Scorecard is a management method A Balanced Scorecard summarizes the information of a company that is really important for strategic development. Balanced in the scorecard means balance in three ways:
-
in the presentation of the company,
-
in the inclusion of all essential organizational units,
-
in the communication with all employees.
With the Balanced Scorecard the following five intentions are pursued:
-
Capturing the complexity of operations and reducing it to partial aspects that are transparent to all employees,
-
Making visions and the strategic goals derived from them measurable,,
-
Communicate these strategic goals to every employee,
-
Anchoring strategies in the daily business (=> budget),
-
Adapting strategies to changing living conditions.
(Quelle: Balanced Scorecard - mehr als ein Kennzahlensystem Frieda, Herwig R., Schmidt, Dr. Walter)
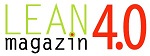
The graphical representation of the work breakdown structure, which divides the project hierarchically into subtasks and work packages on different levels, is called tree structure. On the highest and first level the task/project is always listed. Subtasks and work packages follow on different levels (branches). See also: Work breakdown structure (WBS)
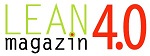
Federal Association of German Management Consultants
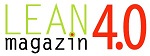
The primary task of container management is to optimize the demand and use of returnable containers and load carriers in order to achieve stable processes and cost savings. To this end, the container flows between suppliers, customers and service providers are coordinated. The basis for the optimization of the volume flows is a well-founded data basis, which is generated by the use of specially developed container management software. Account management based on manual bookings and/or Auto ID RFID solutions creates the necessary transparency for the optimal control of container flows and thus significantly reduces inventory levels, throughput/turnaround times and shrinkage.
(Quelle: www.comepack.com)
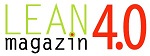
Definition according to Heib and Daneva: Benchmarking is a management tool for determining and delimiting organizational changes. It is the continuous evaluation of own company objects by comparison with best in class or with quantified standards. Benchmarking aims at securing or regaining the own competitiveness of a company.
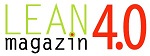
Der Berichtsplan bietet eine Übersicht über alle im Rahmen einer Projektabwicklung zu erstellenden Berichte, ihre Form, Erscheinungstermine, Umfang, Ersteller und Empfänger. Die Berichte kann man innerhalb des Planes in auftraggeberorientierte (z.B. Status Report) und interne Berichte (z.B. Situation report) untergliedern.
(Quelle: GPM)
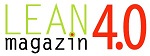
Target group-oriented, needs-based information of all project participants about the project processes, especially for steering committees and documentation
(Quelle: GPM)
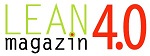
Largest cost item, comprising all materials, supplied parts, work in progress and those end products that have not yet been resold to the customer.
(Quelle: TBM Consulting Group http://www.tbmcg.com/de/about/ terminology.php)
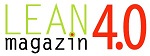
The participant analysis serves to examine the various interests, motives, attitudes, behavioral patterns, etc. that arise in the project, which should thus be included in the planning, goal setting, implementation and evaluation of projects. By interviewing key persons, by working in a peer group or by means of structured questionnaires, the formal and informal groups, institutions and persons involved in the project can be identified, as well as their relationship to each other. These characteristics can be visualized in a table, a relationship matrix or as a map. Additional project goals and activities, but above all possible consequences for the project can be derived from the analysis of participants.
(Quelle: Gabler Management)
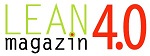
An appraisal team decides on personnel issues such as hiring, promotion and salary changes. Since the assessment of a candidate is a complicated process due to the variety of human aspects to be considered, the decision is delegated to a homogeneous ad hoc team whose overall judgement (compilation of all individual statements) is more objective and meaningful than the opinion of an individual examiner.
(Quelle: Schneider: Lexikon zu Team und Teamarbeit)
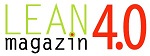
A reference configuration reflects all technical documents of a product and thus its configuration at a certain point in time. It is an essential element in determining the configuration and forms the basis for further activities (e.g. determining deadlines and costs, etc.).
(Quelle: GPM)
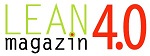
The black box method (method of the black box) serves to make the complexity of systems manageable. One considers the system as a black box by ignoring its inner structure for the time being. The control mechanism within the object under consideration is built into the overall system as a black box, unless one knows how it works or it is opaque. By considering the logical and statistical relations between the input information (Input) and the output information (Output) one tries to draw conclusions about the opaque or invisible control mechanism within the black box. This leads to a reduction of the various conceivable behaviors to a small selection.
(Quelle: GPM)
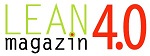
Work areas or stations in production that reduce production throughput
(Quelle: TBM Consulting Group http://www.tbmcg.com/de/about/ terminology.php)
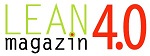
Business process management is the active operation of a business process model, i.e. the holistic management of all processes running in the company, including the consideration of interfaces to the outside world (e.g. to suppliers, outsourcers, customers). This includes all process-related, organizational and controlling aspects in relation to the business processes. If you follow this definition, it quickly becomes clear that BPM is more than just the description of business processes in any way. See also: Business Process Management Business Process Management.
(Quelle: dms-akademie.com)
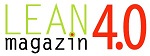
Brainwriting or also 635-method was developed by Bernd Rohrbach. This method is based on the knowledge that proposed solutions are always particularly successful when other participants take them up and develop them further. The rules are: Take a group of 6 participants, for example, who write down 3 ideas in one column each on a prepared form on which the problem is described (3 ideas per participant and sheet). Then the sheet is passed on to the left neighbor, who again writes down 3 ideas, which e.g. associatively or logically systematically build on the ideas on the sheet. This is repeated exactly 5 times. Afterwards the ideas are evaluated. The procedure for the evaluation can be the same as for brainstorming .
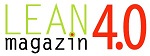
Stations or processes that reduce the production output of the entire system.
(Quelle: TBM Consulting Group http://www.tbmcg.com/de/about/terminology.php)
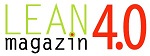
"Bulletin board" on which callers leave their messages. If, for example, customer inquiries land on a bulletin board, they can be read by several people until the responsible employee answers and removes them. This avoids the repeated processing of similar inquiries.
(Quelle: Report Wissensmanagement: Wie deutsche Firmen ihr Wissen profitabel machen Herausgeber: Prof. Dr. C.H. Antoni, Dr. Ing. T. Sommerlatte)
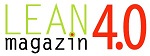
Business process management is the active operation of a business process model, i.e. the holistic management of all processes running in the company, including the consideration of interfaces to the outside world (e.g. to suppliers, outsourcers, customers). This includes all process-related, organizational and controlling aspects in relation to the business processes. If you follow this definition, it quickly becomes clear that BPM is more than just the description of business processes in any way. See also:
Business Process Management.
(Quelle: dms-akademie.com)
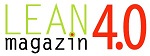
C
This term falls into the area of project controlling and describes the determination of the financing process of a project. One sets an observation period, within which the financially produced surplus of the business activity/project is expressed by the key figure cash flow. This shows the financial resources available to the company during the current sales process to cover the repayment of principal, investment expenses, etc., whereby the current operating expenses have already been deducted within the cash flow. The controller must be aware that the cash flow indicator only reflects the cash inflows and outflows during a period, not the capital available at the balance sheet date.
(Quelle: Mehrmann/Wirtz)
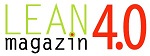
see Critical Chain Project Management
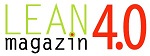
Arrangement of the machines according to the actual process sequence. The machine workers stay in the cell and the material is handed to them from outside the cell.
(Quelle: TBM Consulting Group http://www.tbmcg.com/de/about/ terminology.php)
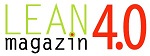
Describes a work cell in which the parts are automatically unloaded from the machines so that the machine operators only need to operate and can continue working on the next machine without waiting. Japanese for shop-load.
(Quelle: TBM Consulting Group http://www.tbmcg.com/de/about/ terminology.php)
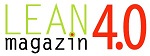
An employee whose task it is to get away from the current status, i.e. batch production with the associated waiting times, in order to achieve a new ideal status: Lean manufacturing. Someone who leads the cultural change in the company.
(Quelle: TBM Consulting Group http://www.tbmcg.com/de/about/ terminology.php)
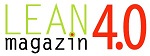
Also transformation management. Refers to the systematic planning, management and control of major changes in organizations. Change management often places high demands on internal communication and the management of resistance.
(Quelle: VDI Nachrichten Nr. 41)
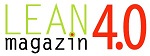
Further development of the call and service center. CICs integrate customer service, support, complaint management, outbound sales, marketing activities and sales management.
(Quelle: Reinhold Rapp: Customer Relationship Management Campus 2000)
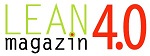
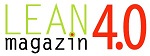
In this method of brainstorming, the project manager or controller creates a notebook in which he explains the problem on about two pages. He then creates a list of people who should receive the notebook in the desired order. Each employee then enters his or her suggestions for solutions and statements in the Note Book and passes it on to the list of people.
(Quelle: Mehrmann/Wirtz)
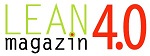
Interaction of computer and telephone technology to produce new services. E.g. automatic call distribution (ACD) or voice recognition
(Quelle: Reinhold Rapp: Customer Relationship Management Campus 2000)
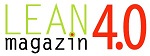
Stationen oder Prozesse, die die Produktionsleistung des gesamten Systems mindern.
(Quelle:TBM Consulting Group http://www.tbmcg.com/de/about/ terminology.php)
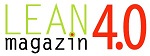
The commitment to improve products, workplace conditions and company reputation day by day.
(Quelle: TBM Consulting Group http://www.tbmcg.com/de/about/ terminology.php)
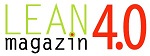
Controlling comes from the English language and means to control. It is a results-oriented, future-oriented corporate management based on a reporting system adapted to specific requirements.
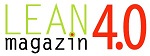
Critical-Chain-ProjectManagement (CCPM) is a project management method based on the theory of Constraints (ToC), which tries to avoid harmful multitasking, i.e. WiP (Work in Progress) is kept as low as possible and in a multi-project environment all projects are staggered in such a way that the previously identified bottleneck of the overall system is optimally utilized.
A special feature of the CCPM is the buffer management, which is aligned to the so-called critical chain. Buffers are much smaller than in classical project management and are located as a large block at the end of a project or as smaller blocks in front of the bottleneck resource so that it never has to wait until the start of its work and is optimally utilized. Thus a high adherence to schedules is achieved, allegedly of 95% despite a reduction of the project duration by 25%. CCPM is similar in its basic principles to Scrum, which is why these methods can be combined well with each other.
(Quelle: Alexander Kriegisch, Scrum-Master.de Siehe auch: Wikipedia - CCPM "Scrum und CCPM - zwei Erfolgsmodelle mit gemeinsamen Wurzeln")
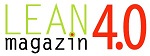
The Critical Path Method (CPM) is based on an activity arrow network diagram (VPN) and is very similar to a bar chart, which is why it is also recommended for non-experts. Developed in the USA in 1957 by the companies E.I. Du Pont and Remington, it is considered the first network plan method. Its main purpose is to determine the critical path on which the events / activities are arranged in such a way that the total time span between the earliest and latest position of an event / activity (buffer time) is minimal. Thus, monitoring measures can be concentrated mainly on these activities and a safe project flow can be guaranteed.
(Quelle: Mehrmann/Wirtz)
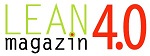
Customer Relationsship Management The management of customer relationships.
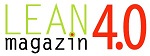
Interaction of computer and telephone technology to produce new services. E.g. automatic call distribution (ACD) or voice recognition.
(Quelle: Reinhold Rapp: Customer Relationship Management Campus 2000)
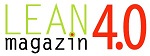
Further development of the call and service center. CICs integrate customer service, support, complaint management, outbound sales, marketing activities and sales management.
(Quelle: Reinhold Rapp: Customer Relationship Management Campus 2000)
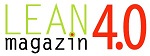
Customer Relationsship Management: The management of customer relationships.
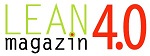
Tailor-made adaptation of products and services to customer expectations. The aim is to expand the relationship with the customer through personalized provision.
(Quelle: Reinhold Rapp: Customer Relationship Management Campus 2000)
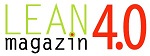
The time required by a machine operator to complete a job. Usually the time until the cycle starts again from the beginning. See Employee cycle time, Machine cycle time.
(Quelle: TBM Consulting Group http://www.tbmcg.com/de/about/ terminology.php)
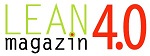
D
Ideally a central collection and distribution point for information. Data sources are brought together on a central platform, prepared in a form suitable for data analysis and made available to users. If an employee is looking for specific information, he or she defines criteria according to which agents browse the data pool. The result can be forwarded to a printer, e-mail or cell phone.
(Quelle: Report Wissensmanagement: Wie deutsche Firmen ihr Wissen profitabel machen. Herausgeber: Prof. Dr. C.H. Antoni, Dr. Ing. T. Sommerlatte)
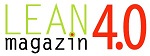
Definition according to DIN: The duration is the time span from the beginning to the end of an operation.
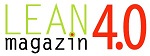
The delegation principle is the transfer of autonomy for action and decision-making in a specific area. Real delegation is only possible if responsibility is transferred and independence exists, otherwise it is only an instruction. Advantages arise from:
-
Employee development
-
Use employee skills
-
Increased productivity through employee satisfaction
-
Increase of motivation
-
Relief of the manager
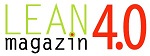
This forecasting method is based on the assumption that a complex problem can be better analyzed and solved by several experts than by a single one. The Delphi technique involves confronting ten to twenty experts with a problem independently of one another using standardized questionnaires and obtaining their opinions. This questioning takes several rounds (usually three to four), which is why this procedure is very time-consuming. Each expert gives his assessment separately and anonymously until a modified, sufficiently homogeneous group opinion (Delphi judgement) can be identified. In contrast to the creativity oriented in brainstorming the Delphi method focuses on reducing an individual opinion to a group assessment.
(Quelle: Mehrmann/Wirtz, Gabler Management, GPM)
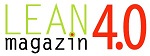
The dialog is an interrelation for example between:
-
Human-Human
-
Human-Machine
-
machine-machine
A direct reaction is generated during the dialog, so that queries can be made immediately in case of ambiguities.
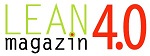
The ability to engage in dialogue is the ability to represent and present one's own points of view and ideas convincingly. As well as a tolerant attitude towards the opinions, viewpoints and peculiarities of others and the ability to deal with them objectively.
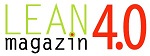
Deutsches Institut for Normung e.V. Monopoly Office for Standardization in German Industry
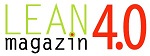
Diviserty (German: Vielfalt) is a concept of corporate management not only to tolerate but also to promote differences among employees. At all levels, the appreciation and benefit of the individual differences of each employee is utilized. Diversity is a concept for promoting and utilizing the diversity of cultures and heterogeneous age structures in the company.
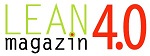
(Diviserty = German: Vielfalt) Diversity management is a corporate philosophy that aims to promote diversity in the workforce. It is the targeted integration of employees of different genders, skin colors, languages, nationalities and religions and serves to make use of different talents and a common understanding.
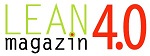
Systematic compilation of information about the project result (as-built documentation, user/operator documentation) and its development process (developer documentation).
(Quelle: GPM)
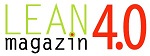
Systems that capture and store knowledge that is already largely available in electronic form through office automation. Special methods of "information retrieval" make it possible to search for and browse through large document inventories in a structured manner.
(Quelle: Report Wissensmanagement: Wie deutsche Firmen ihr Wissen profitabel machen. Herausgeber: Prof. Dr. C.H. Antoni, Dr. Ing. T. Sommerlatte)
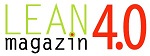
All activities, work packages, subtasks and events with their respective planned dates are combined to an implementation plan, which, after all the usual coordination and approval processes, forms the legal basis for the implementation of the project. It must be familiar to all persons involved in the project, either in its entirety or, if it is too extensive, in parts that apply in each case. From this implementation plan, the further planning documents of the project should be developed, e.g. the time-related cost, expenditure and financing documents as well as the resource planning.
(Quelle: GPM)
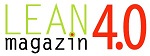
The time it takes to manufacture a single product, from the customer order to delivery.
(Quelle: TBM Consulting Group http://www.tbmcg.com/de/about/ terminology.php)
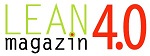
The speed at which the entire system generates money.
(Quelle: TBM Consulting Group http://www.tbmcg.com/de/about/ terminology.php)
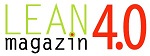
E
E-collaboration tools provide an Internet-based platform for group work. The software usually offers team functions that facilitate joint work. Features for project planning, control and monitoring are often included in the solutions. In addition, e-collaboration tools enable central storage and administration of documents as well as joint document processing with versioning and release functions. Search functions are standard so that the jointly stored information can be found again. Classic groupware functionalities such as messaging, shared calendar management and scheduling are also included. Other features include moderated and unmoderated discussion forums, e-conferencing and e-learning.
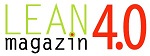
The reduction of makeready work to a single work step.
(Quelle: TBM Consulting Group http://www.tbmcg.com/de/about/terminology.php)
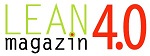
Definition according to DIN: Resources are personnel and material resources that are required to carry out procedures, work packages or projects.
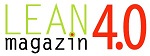
Definition according to DIN: The resource inventory is the number of resources of one or more resource types available at a given time.
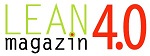
Definition according to DIN: The resource type is the entirety of resourceswhich are grouped according to certain characteristics common to all, such as material characteristics (e.g. type of material), technical characteristics (e.g. test facility), functional characteristics (e.g. properties), professional qualifications (e.g. programmer, locksmith).
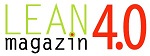
Definition according to DIN 69902: The expenditure of resources is the total expenditure of a resource typewhose temporal position of use has not yet been determined.
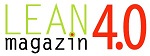
Definition according to DIN: The input material requirement is the quantity of input materials required to achieve the work result at a certain time or within a certain period of time.
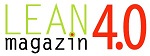
Definition according to DIN 69902: The input resource capacity is the quantity of units that can be generated by the use or consumption of an input resource in a time unit (e.g. an excavator can excavate 100 cbm in one hour).
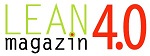
Determination of the required resources and their allocation for the entire project and the individual processes, their effective management and control.
(Quelle: GPM)
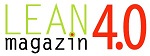
Changeover of a machine in less than 10 minutes: the time between the last good part of a series to the first good part of the next series applies. Synonym: "Single-digit setup time".
(Quelle: TBM Consulting Group http://www.tbmcg.com/de/about/ terminology.php)
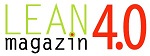
A production concept in which only one part at a time moves from one workstation to the next, without the possibility of stocks forming in between.
(Quelle: TBM Consulting Group http://www.tbmcg.com/de/about/ terminology.php)
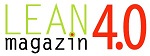
Time that is available within the standard work for a single work step.
(Quelle: TBM Consulting Group http://www.tbmcg.com/de/about/ terminology.php)
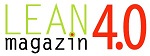
Emergentive (sich hervortuende) Kreativität ist die höchste Form der Kreativität. Aus eigenen Erfahrungen und Erkenntnissen wird etwas Neues, etwas Aussergewöhnliches geschaffen. Siehe auch: Innovative Creativity, Expression Creativity, inventive-Creativity
.
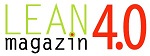
A final sequence is a possible relationship between activities within a network. It exists when the end of an activity is dependent on the end of its predecessor (DIN definition).
(Quelle: GPM)
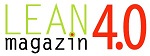
Engineering is a word taken from the American language and originally describes all the activities of a classical engineer, but was then transferred to other areas such as software engineering, information engineering and business engineering.
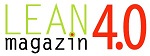
Work areas or stations in production that reduce production throughput
(Quelle: TBM Consulting Group http://www.tbmcg.com/de/about/ terminology.php)
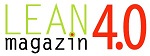
See Theory of Constraints
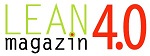
Processes, software and tools to support the marketing process. EMA includes, for example, address generation, campaign execution, but also forecasting and planning functions.
(Quelle: Reinhold Rapp: Customer Relationship Management Campus 2000)
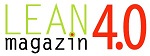
See Steering Committee
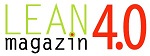
In a decision tree, the possible or already occurred initial situation of a project forms the starting point of the decision making process. Different alternatives for action are conceivable, which entail different consequences. From this one can now derive subsequent situations that represent new starting points for further action alternatives. In order not to let the decision tree grow into infinity, one determines a time horizon or a number of steps as abort criterion, since the probability of occurrence of the regarded situations decreases with increase of these two components. A decision tree should only be used for clear scenarios and interdependent alternatives/situations.
(Quelle: Gabler Management)
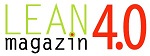
A decision matrix establishes a relationship between all possible situations of a project and the proposed action alternatives. The header of the matrix contains the relevant situations, the header column lists the solution alternatives, excluding of course unsuitable combinations. The cells within the matrix now offer weighed consequences, which for each individual situation form the starting point for an evaluation and hierarchical structure of their action alternatives. This approach to decision making is appropriate when the different scenarios are manageable and the alternatives are of equal importance.
(Quelle: Gabler Management)
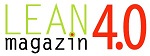
A decision-making team consists of members of the management and the relevant divisional managers. Their task is to formulate the problem, set deadlines and discuss alternatives for solving the problem. It can decide on the alternative solution to be implemented.
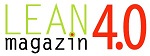
An event is a sequence element that describes the occurrence of a certain state (definition according to DIN 69900). Thus, it has no temporal extension, in contrast to the state it causes. For a project, however, the time of occurrence of the event and thus the achievement of a state is important.
(Quelle: GPM)
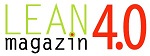
Definition according to DIN: The EKN is a network diagram according to a procedure in which mainly events are described and represented by nodes.
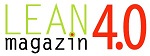
Definition according to DIN: The EON is a network diagram which is exclusively characterised by the description of events (independent of the form of representation).
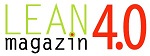
Inventive creativity is the ability to recognise the similarity between two different things and to create something new from it. Although this does not lead to technological breakthroughs, it does create new applications for known principles. See also: Expression Creativity, Productive Creativity, Innovative Creativity.
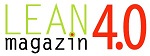
Definition according to DIN 69900: A substitute relationship is a relationship between two events which represents the paths no longer shown in the network aggregation.
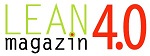
Definition according to DIN 69900: A replacement process is a process that represents the processes replaced between two specific nodes.
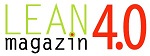
In this special project cost forecasting procedure, the costs incurred by a project are added to the new estimate (Estimate To Completion) of the work still to be performed. The estimate is based on findings that are only gained during the course of the project, e.g. due to necessary changes. The sum of both cost factors (costs incurred + estimated costs) represents the probable total costs of the project (Estimate At Completion).
(Quelle: GPM)
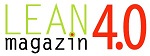
Evolutionism also calls for the following approaches to be added to the traditional linear cause-and-effect principle: self-reference approach, self-organisation, ultra-stability, reactions or interactions, circular causality (cybernetic approach), polycausality (multidimensional approach), random variability (stochastic approach), dynamics (process approach, inclusion of pre-causes/after-effects).
(Quelle: GPM)
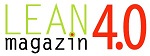
Expansionism means that each object of observation must
(Quelle: GPM)
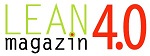
Individual operations during tool change, which can also be carried out under safe conditions during the machine cycle.
(Quelle: TBM Consulting Group http://www.tbmcg.com/de/about/terminology.php)
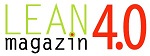
Individual operations during tool change, which can also be carried out under safe conditions during the machine cycle.
(Quelle: TBM Consulting Group http://www.tbmcg.com/de/about/terminology.php)
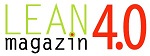
F
One speaks of face-to-face communication when employees exchange the latest information and data on a project or task in conversations that have no official character.
(Quelle: GPM)
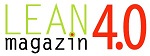
A technical meeting takes place between the employees of a company entrusted with the technical execution of the project tasks and participants from other institutions as required. It regulates the distribution of the technical tasks of a sub-project among the responsible persons.
(Quelle: GPM)
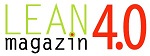
The Failure Mode and Effects Analysis is actually a procedure for quality assurance of production and administration. Its formal principle is used in project management to translate uncertainties and risks into calculable processes. This is done with the help of tables, the first column heading of which often names the process to which a failure refers. The type, cause, probability of occurrence and consequences of the possible disruption/imponsibility are also listed in separate columns.
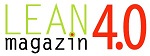
Definition according to DIN 69900: The detailed network plan is a network plan whose structure allows an insight into many details of the project process. It is developed from the outline network plan by increasing the number of roughly executed events, activities or their relationships while maintaining the flow structure, e.g. by refining several activities of the rough network plan using a subnetwork plan. In doing so, one first considers the early activities, then the late ones in the course of the project. A fine network plan can replace or supplement the outline network plan. In the latter case the two plans must also be coordinated during the project.
(Quelle: GPM)
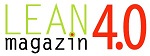
DIN definition: The percentage of completion is the ratio of the work performed as of a reporting date to the total work performed in an activity or project.
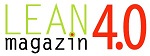
This method of effort estimation is very imprecise. The work value of a work package is determined depending on the estimated degree of production. Many subjective factors of the people involved in the project are taken into account.
(Quelle: Mehrmann/Wirtz)
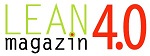
The stage of completion is the service planned or rendered at a given point in time, whereby this concept of service must be distinguished from that used in resource accounting (see service).
(Quelle: GPM)
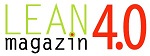
DIN definition: Completion value is the cost of an activity or project corresponding to the stage of completion. entsprechenden Kosten eines Vorgangs oder Projektes.
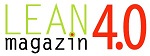
see Ishikawa diagram
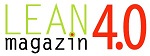
A research and development project involves intellectual, creative and experimental work, the aim of which is to gain new, not yet available knowledge. The project objectives of this type of project deliberately exceed the current state of research in science and technology. Such projects include, for example, the development of new products or the design of new software etc.
(Quelle: Mehrmann/Wirtz, GPM)
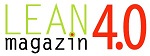
Definition according to DIN: The Free Buffer Time is the period of time by which an event or process can be shifted from its earliest position without affecting the earliest position of other events or processes.
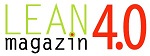
Definition according to DIN: The Free Reverse Buffer Time is the time span by which an event or process can be shifted with respect to its latest position without affecting the latest position of other events or processes.
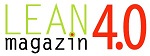
In a free interview, there is no prescribed catalogue of questions that determines the order, topics or formulation of the questions. The interviewer, for whom a good qualification is a prerequisite, can lead the interview with a view to the objective of the investigation and respond to the person interviewed. A free interview is usually open, flexible and lively, but it takes a long time and is therefore a costly affair. Moreover, such interviews usually depend on one or a few interviewers, are difficult to evaluate and are strongly influenced by the interviewer and his counterpart, so that objectivity is not always maintained. The use of free interviews may be appropriate during an exploration phase in order to gain an overview of the object of investigation.
(Quelle: Mehrmann/Wirtz)
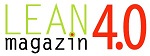
This human quality enables a person to cope with seemingly hopeless situations, severe disappointments and setbacks, as well as to react to recurring or shock-like frustration in a reasonable way. Frustration tolerance can be promoted through targeted training.
(Quelle: Schneider: Lexikon zu Team und Teamarbeit)
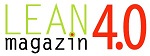
Leading means steering cooperation, social action and creating optimal motivational conditions.
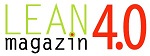
Leadership is to be understood as the goal-oriented influencing of employees' behaviour. The project manager is responsible for ensuring that the task assigned to him and his project staff is completed or the set goal is achieved.
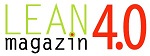
This management concept envisages that the various management tasks of a team are performed by two people, a relationship specialist and a task specialist. In this way, the permanent balance between the internal cohesion of the team and its performance is to be maintained.
(Quelle: Schneider: Lexikon zu Team und Teamarbeit)
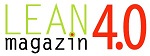
Management principles are the written definition of general management tasks that apply equally to managers and employees. The leadership principles describe the spirit of leadership and thus comprise the corporate principles and objectives from which an optimal leadership organisation is derived. Leadership principles provide the basis for the overall assessment of managers at all levels with regard to the fulfilment of their management tasks.
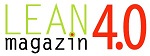
Management instruments enliven the management principles. Their consistent application is the key to leadership quality in practice. Management instruments for communication are e.g:
-
Delegation technology
-
Decision making
-
Conference management
-
Staff appraisal
-
Employee information
-
Dialogue
-
suggestion scheme
-
Complaints procedure
-
Conflict regulation
-
Management Conferences
Management instruments for employee development are, for example
-
ssessment centre for internal executive selection
-
Succession planning
-
Trainee programmes
-
Employee assessment
-
Staff appraisal
-
Staff recruitment procedure
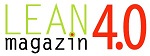
Managers are employees with specific tasks and perform management functions. They can do this either as superiors, staff members or as people who are equipped with information and advisory skills without leading themselves.
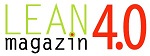
Management organisation refers to how a company has organised itself in order to lead itself and its employees to success.
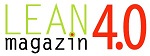
The quality of leadership is usually the deciding factor between success or failure - not the market. Therefore, the quality of leadership is one of the most important characteristics in a company.
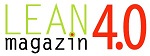
This method of calculating project expenditure is mainly used to estimate projects in the IT sector. Based on the determination of functions, their evaluation and the quality to be provided, so-called function points are created. These are then transferred into a function curve. In the first step of the process, the business transactions are evaluated in the categories light, medium, complex and assigned a number between 3 and 15 to each size. These function points of the business transactions are added together (total 1).
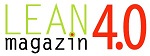
A function chart is presented in matrix form and assigns specific tasks to persons/positions. It is divided into a horizontal header line, which lists all the persons/positions involved, and a vertical header column, which lists all the tasks to be performed. Each field of the matrix uses abbreviations or symbols to indicate the function (e.g. decision, control, execution, etc.) assigned to each person/position in relation to a specific task. Thus, each individual column shows the involvement of a person/position in the processing of all tasks. The lines record the division of labour, i.e. how many persons/positions are involved in the execution of a single task. In the multi-level form of a function chart, the header column contains not only individual tasks but also task areas consisting of several tasks. The header also shows the hierarchical relationships of superiority and subordination, from which the overall competence and responsibility can be derived. The function diagram provides a quick insight into the project planning, but if personnel shifts are made, it is no longer meaningful. Nor does it reveal information and communication relationships.
(Quelle: Gabler Management)
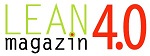
This is the form of a work breakdown structure, in which the project object loses its contours and the tasks for planning and implementing the project are in the foreground. See also: Work breakdown structure (WBS)
(Quelle: GPM)
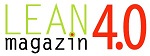
This method of calculating project expenditure is mainly used to estimate projects in the IT sector. Based on the determination of functions, their evaluation and the quality to be provided, so-called function points are created. These are then transferred into a function curve. In the first step of the process, the business transactions are evaluated in the categories light, medium, complex and assigned a number between 3 and 15 to each size. These function points of the business transactions are added together (sum1).
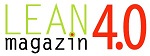
G
The GANTT technique (Henry Lawrence Gantt), which can also be described as a simple bar chart technique, simplifies scheduling by providing a graphical representation. The individual processes are plotted along a time axis in accordance with their duration. The disadvantage is that the scheduling dependencies are not recognisable. The GANTT technique is seldom used, when a visually convincing form of presentation is required for project scheduling with few project parts. See also: Listing technology, PLANNET Technology.
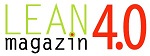
Gemba comes from Japanese and means: crime scene - place of action. Gemba is where profits are made or losses occur! With small means almost every stage of production can be freed from non-value adding processes. The way does not lead via costly automation projects, but via small, practically realisable steps to a flexible, lean production in manufacturing. The Gemba is the source of ideas for improving quality, costs and delivery. Kenishi Sekine (the Gemba Pope) has been involved in the organisation of "lean factories" and the rapid increase of productivity for more than 30 years. He is known in professional circles as the "pope" for the optimisation of production processes. Numerous books and publications underline his expertise and reputation. The use of Gemba in organisation and administration is still new and is developing rapidly at the moment. The continuous improvement in the office releases undreamt-of potentials. The reduction of lead times and improved added value of all processes saves a lot of time and money.
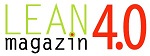
Overheads are all costs incurred in a company for general administration, sales, etc. The manufacturing costs of a product must be allocated to them proportionately using the apportionment method in order to calculate the sales costs.
(Quelle: Madauss: Projektmanagement)
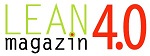
The term Overall Equipment Effectiveness (GAE) is a key figure developed by the Japan Institute of Plant Maintenance. It is one of the results of decades of development of the TPM concept (Total Productive Maintenance). Overall Equipment Effectiveness is a measure of the added value of a plant. The GAE of a plant is defined as the product of the following three factors:
-
Availability factor
-
Power factor
-
Quality factor
Their value range is between 0 and 1 or between 0 % and 100 %. World-class companies achieve an OEE of 85% from an operational perspective in the manufacturing industry and 95% in the process industry from an operational perspective. GAE is defined as the product of availability factor, performance factor and quality factor. Thus follows: GAE = availability factor x power factor x quality factor A percentage value results, indicating the percentage of the planned machine running time that has actually been produced. In most cases this value is clearly below 100 %, because the factors involved are mostly below 100 %. In this way, a wide variety of wastes are made clear. The benefit of GAE consists in the reliable analysis of machine time losses, exact calculations and evaluation possibilities, consideration of interfaces and interdependencies and thus lets the management look at the plants with a different view.
(Quelle: Wikipedia.de)
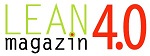
Definition according to DIN: The total buffer time is the time span between the earliest and latest position of an event or process.
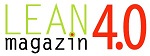
Business process management is the active operation of a business process model, i.e. the holistic management of all processes running in the company, including the consideration of interfaces to the outside world (e.g. to suppliers, outsourcers, customers). This includes all process-related, organisational and controlling aspects in relation to the business processes. If one follows this definition, it quickly becomes clear that BPM is more than just the description of business processes in any way.
(Quelle: dms-akademie.com)
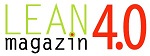
An extension of the Toyota production system and a strategy to introduce lean manufacturing trough Kaizen einzuführen.
(Quelle: TBM Consulting Group http://www.tbmcg.com/de/about/ terminology.php)
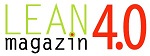
According to Ferschl, graph theory is a mathematical discipline that serves to determine similar structures in a number of different empirical situations and to study and document their regularities.
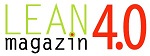
The primary task of groupware is to network people or work groups that work together at different times or at different locations.
(Quelle: Report Wissensmanagement: Wie deutsche Firmen ihr Wissen profitabel machen. Herausgeber: Prof. Dr. C.H. Antoni, Dr. Ing. T. Sommerlatte)
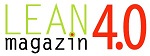
H
Hancho comes from Japanese and stands for a group leader. With the introduction of the Hancho function (team leader level), Toyota has achieved enormous increases in productivity and quality. In his role as process observer and manager, he is responsible for the daily improvement process in his team. A Hancho must have high social competence in order to successfully coach and lead his employees. The most important lean tools of the hancho are
-
Leading successfully with target states
-
Solving problems systematically with PDCA
-
Develop and monitor standards
-
Visuals Management
-
Problem solving techniques
-
Daily CIP
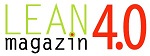
A device by which finished parts are automatically removed from the machines. This eliminates the waiting time for the machine operator to intervene.
(Source: TBM Consulting Group http://www.tbmcg.com/de/about/terminology.php)
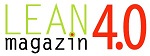
Production smoothing or levelling. Sequential work planning determined by the average demand for parts.
(Quelle: TBM Consulting Group, http://www.tbmcg.com/de/about/ terminology.php Tool Anbieter: Kanbantafeln/Heijunka Tafel)
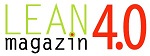
The cost of goods manufactured comprises the various direct costs incurred in the manufacture of a specific product, e.g. costs of development, production, etc. Overhead costs and profit are not included.
(Quelle: Madauss: Projektmanagement)
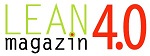
A heterogeneous team consists of specialists and experts who are distinguished by their qualifications and previous training in various fields of knowledge.
(Quelle: Schneider: Lexikon zu Team und Teamarbeit) Seminaranbieter: Team-Management mit der elektronischen Matte)
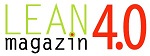
Hierarchy is a hierarchy of rank. The hierarchy in the organizational plan describes the superordinate and subordinate relationships. It can be represented as a building diagram. The trend is more and more towards flat hierarchies. Problems arise when a company finds itself in a dynamically changing environment where creativity and flexibility are needed.
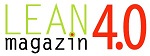
A homogeneous team is made up of experts and specialists with largely similar technical training and qualifications.
(Quelle: Schneider: Lexikon zu Team und Teamarbeit Seminaranbieter: Team-Management mit der elektronischen Matte)
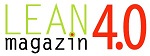
Hoshin Hoshin is a term that comes from the Japanese with Chinese origin and means compass needle (composed of the word "ho" = direction and "shin" = needle). In Japanese industry the term "Hoshin Kanri" is often used. "Kanri" means "management", "planning", therefore the synonym Hoshin planning. Hoshin Kanri (Management by Policy, Policy Deployment) is a company-wide planning and control system,
-
That involves all managers and employees
-
In a systematic and stringent cascading (derivation and coordination) process
-
As part of a simultaneous vertical and lateral (horizontal) coordination and agreement
-
During which the overall breakthrough goals (breakthrough's) of the company are developed and defined from the vision
-
Derive the most important strategies and goals for all employees (including managers)
-
To ensure that the aspirations of all employees of the company are focused on the same vision and the same goals
In Germany, this control system is still very little known, even by name. In terms of content, only a few companies are familiar with it and usually only those that are primarily associated with HP or with (former) managers of this company in business relationships or as executives.* Hoshin-Kanri contains a target hierarchy. The multi-annual goal (Ideal or Vision) is the North Star (True North), which is used as the basis for the annual goals, but also for the concrete improvement activities. Because the North Star is aligned with customer needs, the previously different and sometimes contradictory management objectives can be redefined, synchronised and coordinated. This resolves some of the previous conflicting objectives.**
*(Quelle: http://www.frankfurt-school.de/dms/Arbeitsberichte/Arbeits14.pdf)
**(Quelle: http://www.wandelweb.de/wiki/index.php5?title=Hoshin_Kanri)
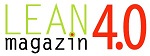
The House-of-Quality is a concept within the framework of quality management that has already proven itself in industrial production - for example in the automotive industry. The aim is to bring product quality in line with customer requirements. To this end, customer orientation is firmly anchored in every phase of product and service development.
(Quelle: BIBB)
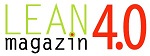
I
Finding ideas is the search for new ways of thinking with the help of creativity techniques. "Nothing is more dangerous than an idea, when it is the only one you have." Emile Chartier
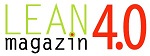
Idea collections such as brainstorming, metaplan techniques, brainwriting etc. are techniques where ideas on a topic are organised and freely collected and written down. The principle is followed: First collect - then evaluate.
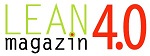
Also known as passive telemarketing, it means the processing of incoming calls. Here, the calls are automatically distributed via the telephone system to the individual telephone workstations - according to the qualifications and workload of the call agents. Typical inbound services include order acceptance, complaints management, information and service hotline, etc.
(Quelle: Reinhold Rapp: Customer Relationship Management Campus 2000)
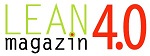
Target group-oriented, needs-based information of all project participants about the project processes, especially for steering committees and documentation
(Quelle: GPM)
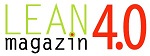
Innovative creativity is the ability to improve existing technologies once the basic principles are understood.
See also: Expression Creativity, inventive-Creativity
, Productive Creativity.
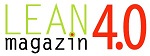
Interaction refers to the mutual relationships between individuals and/or groups mediated by communication, and the resulting influence on their attitudes, expectations and forms of behaviour.
(Quelle: Schneider: Lexikon zu Team und Teamarbeit)
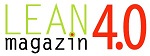
Handles during tool change, which must be performed when the machine is not running.
(Quelle: TBM Consulting Group http://www.tbmcg.com/de/about/ terminology.php)
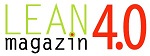
Internet Relay Chat (IRC) is a method for optimising communication between project participants. It enables a virtual meeting of several people and also larger groups to clarify current issues. These meetings via the Internet, which can be held daily if required, allow the involvement of more distant project participants. For the respective employees, there is no need for travel time and longer absence from the actual workplace, as they only have to go to the next computer, so that working time can be saved.
(Quelle: GPM)
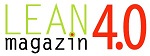
The survey procedure via interview serves to eliminate and reduce knowledge deficits. It is often used in organisational studies as part of a project's as-is analysis. The interview technique is used in empirical experiments with demographic background as well as in sales and market research. In project management, this is understood to mean the targeted, oral interview during the as-is analysis of an organisational project.
(Quelle: Mehrmann/Wirtz)
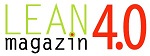
One speaks of interviewer bias when the interviewer consciously or unconsciously influences the interviewee, which is often the case in freely formulated interviews. The answers of the interviewer then turn out differently for different interviewers.
(Quelle: Mehrmann/ Wirtz)
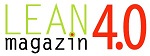
Largest cost item, comprising all materials, supplied parts, work in progress and those end products that have not yet been resold to the customer.
(Quelle: TBM Consulting Group http://www.tbmcg.com/de/about/ terminology.php)
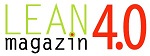
An investment project involves the production, construction or individual acquisition of tangible fixed assets. In the process, financial resources are transferred to property, plant and equipment. An investment project is, for example, the construction of an airport, the building of a new production hall, etc.
(Quelle: Mehrmann/Wirtz, GPM)
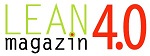
This method, which is named after H. Ishikawa, allows for easy recognition and analysis of the causes and effects of a problem area. Central problems become visible, as well as the interactions of the cause complexes, furthermore the whole problem can be revised in a structured way. The persons involved are brought to understand the problem together. Once the problem has been identified, a diagram is created which uses arrows to assign the causes to their effects and thus to the problem. Since often several different causes cause a problem, the Ishikawa Cause Analysis ranks them according to four influencing variables: Man, machine, material and method. The following phases regulate the procedure with this technique: First the problem is defined, then the main causes are determined. Then there is a brainstorming on the individual causes, the most likely of which are selected. Finally, after a review, one tries to find possible solutions.
(Quelle: Gabler Management)
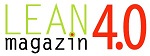
J
Japanese for the transfer of human intelligence to a machine.
(Quelle: TBM Consulting Group http://www.tbmcg.com/de/about/terminology.php)
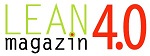
The Jour Fix is a regular, informal discussion group for which the project manager arranges a fixed place and date. Usually there is no formal agenda at this meeting, so that the employees can exchange their experiences with the joint project in a relaxed manner. The project manager is informed about the actual problems and communication between the participants is improved.
(Quelle: GPM)
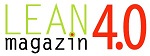
Production according to demand: only what is needed is produced, at the right time and in the desired quantity.
(Quelle: TBM Consulting Group http://www.tbmcg.com/de/about/terminology.php)
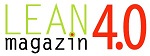
Just-in-time production, or JIT for short, is a form of production management. In this form, parts for the production process are not stored temporarily as usual, but are delivered directly in the required quantity to the intended production location at the right time. The advantage is the great flexibility towards customer requirements and the high readiness to deliver with short delivery times, as well as the production of customer-specific end products without high inventory costs and risks.
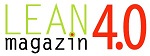
K
Radical improvement, usually of a business process, which has an impact on the future value chain.
(Quelle: TBM Consulting Group http://www.tbmcg.com/de/about/terminology.php)
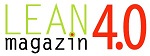
This management principle comes from Japan and means improvement. This principle focuses on the improvement of existing services, business processes, methods, means of production, products, techniques etc. Combination of the two Japanese words Kai (change) and Zen (good). Generally stands for "continuous improvement". In other words, Kaizen means change for the better or further development. Kaizen is a management philosophy that defines the role of management in the continuous promotion and introduction of small improvements that involves every employee. It is a process of continuous improvement in small steps that makes a process more efficient, effective, controlled, and adaptable. The improvements are usually achieved with little or no effort, without sophisticated techniques or expensive equipment. The focus is on simplification, breaking down complicated processes into their sub-processes and then improving them.
Kaizen focuses on:
-
Value-added and non-value-added activities
-
Avoidance of muda (waste):
-
Overproduction
-
Delays
-
Unnecessary transports
-
Waste in the process
-
High inventory levels
-
Wasted movement
-
Defective parts
-
-
Principles of material handling and use of One-Piece-Flow
-
documentation of standard operating procedures
-
The five S's for workplace organisation
-
Creating transparency: Simplify information content and its visual implementation on the relevant communication media
-
Just-in-Time Principles to produce only the units in the right quantities, in time, and with the right means
-
Poka-Joke, prevent or discover errors
-
Dynamic teams that solve problems, have communication skills and master conflicts.
(Quelle: ECO vom 01.09.2008)
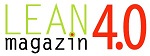
A methodology that attaches great importance to the time factor, can be implemented quickly and is results and team-oriented. Continuous improvement.
(Quelle: TBM Consulting Group http://www.tbmcg.com/de/about/ terminology.php)
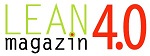
Calendaring is the conversion of a time to a specific calendar date. After the conversion, the point in time is called a date.
(Quelle: GPM)
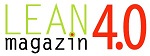
Kanban (jap. for "card", "board") is a way of organising production or process flows according to the pull principle (instead of push). Originally coming from production control, Kanban is now also used in support & maintenance as well as in software development, there often as "Scrum-Ban" as a supplement or modification of the Scrum procedure model. Kanban implements a simple method to minimise the lead time of an element to be produced or a task to be performed by several people and to avoid stock-keeping or piling up tasks by identifying and optimally exploiting bottlenecks. In this respect there are points of contact with the ToC (Theory of constraints)and the CCPM (Critical Chain project management).
(Source: Alexander Kriegisch, Scrum-Master.de; siehe auch: Wikipedia - Kanban Vergleich Kanban vs. Scrum im Software-Umfeld Lieferantenkanban Tool Anbieter: Kanban Software Kanbantafeln/Heijunka Tafel)
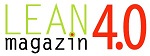
Capacity requirements planning is the determination and projection of the occupancy per time period for a machine, a workplace, a department, a plant...
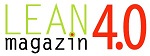
Capacity planning is the part of project planning for the distribution of capacities to subsystems, calendar months/weeks and project phases.
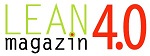
This procedure is used for the division of tasks. One task (object and performance) is carried out at a time, which is noted on a card. The cards are moved along metaplan walls until the optimal sequence of tasks is found. This technique reaches its limits as soon as complex organisational units are to be examined.
(Quelle: Mehrmann/Wirtz)
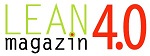
Visualisation tools as alternatives to the purely textual transfer of knowledge, such as graphic navigation aids or hyperbolic trees for displaying hierarchical information structures.
(Quelle: Report Wissensmanagement: Wie deutsche Firmen ihr Wissen profitabel machen. Herausgeber: Prof. Dr. C.H. Antoni, Dr. Ing. T. Sommerlatte)
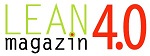
Federal Government Coordination and Advisory Office for Information Technology in the Federal Administration.
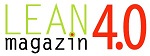
Unter Kernkompetenz versteht man die Zusammenfassung der betrieblichen Qualifikation, die die Grundlage für den Erfolg am Markt bilden.
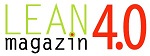
Local Community Agency for Administrative Simplification
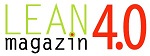
Kick-off events are starting events that serve to clarify the goals for the next period and to motivate. They usually take place at the beginning of the year, at the beginning of a project or at the beginning of a period of upheaval.
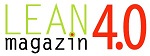
Killer phrases are phrases that prevent any creativity and constructiveness, i.e. kill. That is not our style! Theoretically brilliant, but...! You will never find support for this! No time, and too expensive! Nobody sticks to that! Bullshit! You must explain in detail! That's impossible! You're one to talk! Believe me! That's not the point!
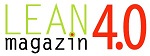
Databases that provide users with information on decentralised servers worldwide. Can be used company-wide via intranet: Collection and provision of daily updated information such as fault reports, error descriptions, service information; forum for the exchange of problem solutions.
(Quelle: Report Wissensmanagement: Wie deutsche Firmen ihr Wissen profitabel machen. Herausgeber: Prof. Dr. C.H. Antoni, Dr. Ing. T. Sommerlatte)
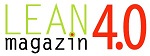
Communication means any kind of message exchange. Between people, communication serves the endeavour for common understanding and joint action as a prerequisite for success.
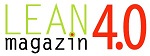
Configuration means all functional and physical characteristics of a product as described in the technical documents - if necessary also in the business documents - and finally realised in the product itself.
(Quelle: GPM)
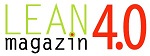
Unter Konfigurationsaudit versteht man die formale Überprüfung einer Konfigurationseinheit bzw. eines Produktes auf Übereinstimmung mit den geltenden Konfigurationsdokumenten.
(Quelle: GPM)
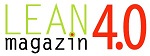
Configuration accounting is the formalised documentation and reporting of the prescribed configuration requirements, the status of ongoing change requests and the implementation status of approved changes. It allows changes to the reference configuration to be tracked. Configuration accounting starts with the initial collection of configuration data.
(Quelle: GPM)
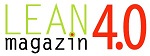
Configuration identification is used to define and verify the structure of products (configuration) in more detail and to identify the products themselves and their documents. From there, changes are controlled, accounting, verification and status reporting are carried out. The technical content identification determines reference configurations and their validity step by step and in coordination with the project phases. They form the basis for possible changes, for cost determination, deadlines, technology assessments, etc. The formal identification structures the product and makes a selection of configuration units (KE). Once the product documentation has been defined, the individual elements are numbered and marked. Finally, product, configuration and documentation trees are compiled, which must be maintained at regular intervals.
(Quelle: GPM)
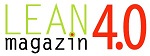
Detailed and complete compilation and documentation of the project results and their systematic updating in case of project changes.
(Quelle: GPM)
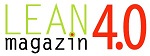
Configuration monitoring consists of measures for monitoring changes made to a specific configuration unit (KE). The configuration documents must already have been formally created for the first time and include change procedures. By means of change management, changes are identified, described and classified. The changes listed in the change request are evaluated, approved or rejected in a conference. A change notification is issued upon approval. When changing the reference configurations, all possible effects (e.g. on technical subsystems, costs, etc.) must be taken into account.
(Quelle: GPM)
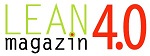
The commitment to improve products, workplace conditions and company reputation day by day.
(Quelle: TBM Consulting Group http://www.tbmcg.com/de/about/ terminology.php)
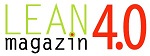
CIP stands for Continuous Improvement Process and describes a method that serves the continuous improvement of process, product and service quality. CIP thrives on the idea that the employee knows his work processes most precisely and can therefore best recognise improvements in the processes. A corporate culture that supports and rewards teamwork and ideas of employees is therefore an important foundation stone for the implementation of CIP. CIP is a method of small steps, but when carried out systematically, consistently and purposefully, it leads to an improvement in one's own process in daily operations. This corporate culture must be exemplified by the management. All levels of the company must work consistently on the following goals:
-
The setting and pursuit of objectives
-
The elimination of faults
-
The search for improvement possibilities
-
The avoidance of waste
Procedure of a CIP:
-
What can be improved?
-
Describing the actual and target state by means of key figures
-
Describe and evaluate problems that occur
-
Evaluate the problems
-
Analysis of the problem (causes, connections)
-
Collection of possible solutions (e.g. in a brainstorming session)
-
Evaluation of the solution ideas and decision
-
Derive the necessary measures, evaluate expenditure and income
-
Presentation of the results to the decision-making body
-
Define measures and clarify resources
-
Implement measures
-
Checking success
To achieve economic success from CIP, it is important to establish this process in the general corporate culture. This requires the creation of the appropriate framework conditions, such as the provision of working time, further training measures, implementation in workflows and processes and, above all, the implementation of ideas. The CIP concept is a systematic approach of planning, implementing, checking and acting (PDCA cycle).
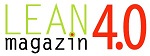
Cost trend analysis is a method of controlling project costs that allows estimates of the total costs of a project to be made regularly for the expected final date. The method focuses on determining the completion value. The estimated value of the total costs is derived from the planned total costs (POC) calculated in project cost planning, the periodically determined actual costs (AIK) and the current Completion value (AFW) of the work packages, from which the following formula can be derived: SGK=PGK (AIK/AFW). The ratio AIK/AFW represents a cost increase factor which is used for the estimate. The calculated estimated value of the total costs is graphically represented by the cost trend curve, the values of which must be commented on. In addition, comments on the deviations from the planned costs are required and possible corrective measures must be taken. The estimated value of the total costs of the project is only a trend assumption, which assumes that the respective development will continue.
(Quelle: GPM, Mehrmann/Wirtz)
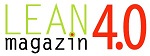
Determination of the costs for the individual work packages and processes as well as for the overall project as a basis for financing, budgeting and controlling of projects.
(Quelle GPM)
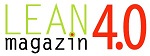
The cost value is an indicator of costs and finances that can be compared with the expenditure value of the resource accounting. It shows the ratio of costs to the work result: cost value = cost/work result.
(Quelle: GPM)
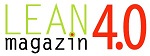
How many euros may the project cost (calculated expenditure).
See also: Project goal, Objectives, Target dates.
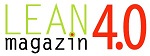
Prof. Dr. Heinz Hoffmann defines creativity as the ability or capacity to form new combinations from two or more concepts existing in the mind. Creativity is a key element in the search for new ideas. One can distinguish 5 different levels
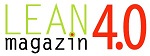
Creativity techniques are methods that serve to generate innovations or several alternative solutions to a given problem. Creativity techniques are e.g. brainstorming, Morphological analysis, Method 635 etc.
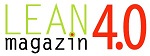
The method of the chalk circle goes back to Taichii Ohno, who from time to time painted a chalk circle on the floor of his factory building. He placed himself in this chalk circle and observed the events in peace. This serves to stand in a "delimited space" and to see what potential for improvement there is in the observed processes. If one succeeds in perceiving the mutual observation not as a control, but as one with and for each other, then the potentials can be tapped in the sense of a common whole. In the sense of knowing yourself, the chalk circle method is an important element in the process of change. Only if you recognise what makes trouble, you can help to make it easier. Helping to make it easy is the task of those who manage the funds. Ergo these should also be included in the chalk circle.
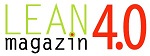
In the field of planning technology, criticality is occasionally used as a key figure. It establishes the ratio criticality = number of critical activities/total number of activities in a network. The higher the criticality, the broader the deadline and thus often the cost risk of the planning.
(Quelle: GPM)
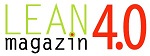
Statement of the German Institute for Business Administration: The customer is not an interruption of our work. He is their goal. In the end, he pays our salary. He is not from us, but we are dependent on him. Therefore, it is not we who do him a service when we take care of him, but he does us a service. He gives us the opportunity to prove that we are in the right place.
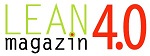
The heart of any targeted marketing application, as the database collects all information about the customers and their interests. Can be used as Data-Warehouse (holistic approach across the entire company) or organised as a data mart (small approach for a single department in the company).
(Quelle: Reinhold Rapp: Customer Relationship Management Campus 2000)
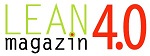
L
Definition according to DIN: The (temporal) position of an event/process is given by the assigned times/dates.
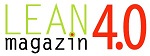
The time it takes to manufacture a single product, from the customer order to delivery.
(Quelle: TBM Consulting Group http://www.tbmcg.com/de/about/ terminology.php)
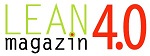
1st term: The term lean banking or lean bank has no fixed definition. In Continental Europe it is rather used as a generic term for quantitative and qualitative optimisation approaches of internal business processes in banks. For this reason, there are voices in the banking industry which, due to a lack of precision in the content of the term Lean Banking, also advocate the term Lean production ,pointing out that it is substantiated by the Massachusetts Institute of Technology's study on the future of the automobile, published in 1990 under the title "The Machine that Changed the World". However, the optimisation concepts contained in this study are tailored to classic production companies. Not all of these approaches can be easily transferred to service companies. It is also necessary to take into account the specifics of the banking industry in terms of sectors and activities. The term lean production does not meet this requirement. Terminologically and in terms of content, Lean Banking in this respect (similar to an analogy) captures the principles of Lean Production that can be transferred to banking business management.
Translated with www.DeepL.com/Translator (free version)
2. characteristics: Lean banking is not a new organisational approach, but rather a structural optimisation that sees the divisionalisation and customer group organisation of the 1980s as a substantial component. The lean bank is characterised above all by
-
Customer group-oriented organisational structure
-
Decentralised management structures
-
Process orientation
-
Reduction of core competences, complexity and value chains
It leads to a measurable increase
-
The quality of services and products
-
Customer satisfaction and loyalty
-
To a sustainable reduction in costs.
(Quelle: Wirtschaftslexikon24.net)
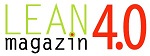
Lean Construction is the adaptation of the Toyota production system to the construction sector. In addition to the term Lean Construction, the term Lean Management is also used in the construction industry. During the creation of a construction project, a continuous process lived out to eliminate waste, to achieve or exceed all customer expectations, to focus on the entire value stream and to strive for perfection. Lean Construction is an integral approach to the planning, design and execution of construction projects. The roots of Lean Construction (LC) lie in
Lean production, which has revolutionised the design and planning of production, procurement and assembly processes in some sectors of the economy. The basis of Lean Construction are approaches of Lean Thinking, which focus on the value-added process in order to maximize value and minimize waste in the processes. Using specific techniques, Lean methods are applied to the planning and execution of construction projects - with the following tangible improvements:
Translated with www.DeepL.com/Translator (free version)
-
The planning and its implementation processes are viewed and designed holistically to better meet the client's needs.
-
Work is organised throughout the process to maximise value and reduce waste.
-
The optimisation efforts focus on improving the overall performance of the project rather than on individual sub-areas.
-
Planning and control systems play an important role and are being improved.
(Quelle: http://de.wikipedia.org/wiki/Lean_Construction siehe auch: Artikel LEANmagazin)
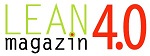
The Lean Initial Audit is a structured collection of knowledge and evaluation of your company's activities. The audit should consist of a series of interviews conducted at different organisational levels depending on the size and complexity of your company. The audit team must assess the current status in all key areas and control points of the work units. LIA is thus the systematic recording of the technological process. The value stream in the actual state for a core product is defined and a documentation of visible waste is prepared (waste walk). A potential analysis and quantitative determination is carried out on the basis of the lean key figures (lean metrics). Without an as-is analysis the lean tools and tools cannot be effective. The Lean Initial Audit should answer the following questions:
-
Where is there potential in the processes?
-
What potential is there in the processes?
-
Which methods and tools can increase these potentials?
Lean Machining is the "lean handling" of machine tools in order to manufacture customer-specific products faster and more cost-effectively. To achieve this, some suppliers have started to treat their shop as a cell. By carrying out several simultaneous customer-specific processes, the cycle time can be drastically reduced. Not only does the product become cheaper, but also the cycle time is reduced. The result is that a quality product can be produced in less time for less money.
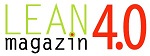
Lean management means "lean management". It is a management concept that aligns the entire company with the principles of lean production. Lean Management is a management approach which is characterised in particular by the basic principles of decentralisation and simultaneousisation. The aim of this approach, both within the company and across the company, is to bring about a stronger customer orientation with consistent cost reduction for the entire company management.
(Quelle: Gabler Verlag (Herausgeber), Gabler Wirtschaftslexikon)
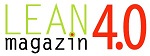
Production of a product with a minimum use of resources (labour, materials, capital, machinery, etc.) and in compliance with the delivery date.
(Quelle: TBM Consulting Group http://www.tbmcg.com/de/about/ terminology.php)
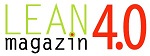
The concept of lean organisation is based on the considerations of lean management and describes a streamlining of the organisation. The following guidelines are characteristics of lean organisation: few hierarchical levels, small organisational units, low division of labour.
(Quelle: http://www.steuerlinks.de/organisation/lexikon/ lean-organisation.html)
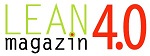
Lean production is based on the following principles:
-
Reduction of the vertical range of manufacture through increased cooperation with partners
-
Return of tasks, concepts and responsibility to the primary service areas
-
Simultanisation: abandonment of Tayloristic function specialisation in favour of holistic processes and integration and parallelisation
-
Informational networking with dealers, forwarders and suppliers
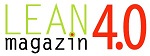
The term "lean" is in full swing. Especially in times of low turnover and contribution margins, organisations strive to be lean. This also applies to their projects and project management. In the process, people tend to forget what "lean" concepts are actually about.
For this reason, this method description shows
-
which is the core of the "lean" idea,
-
how the "lean" idea can be transferred to project management,
-
what the "lean" idea means for project management methods.
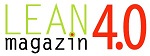
The concept of performance can be viewed from different perspectives. In the resource accounting (DIN 69902), we work with the physical-technical definition: performance is work per time. In this context, performance means achieving a specific work result within a specified time frame. Such a definition completely disregards intellectual, above all creative and communicative achievements which are not time-bound but dependent on their originator and are not directly evident from the result achieved. In the field of cost and performance accounting (DIN 69903), in terms of project management (DIN 69901) and also in progress control, the legal concept of performance prevails. It can be measured to a much greater extent, as it is only defined by actions or omissions, for a project e.g. within the framework of a contract for work and services. The respective control point in time (deadline) has no mathematical significance for performance, but only a delimiting and limiting significance. Often a legal performance corresponds to a technical result of work.
(Quelle: GPM)
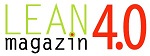
ATask planning: recording and evaluation of the planned individual services regarding quantities and qualities in relation to the project definition (specifications) Process planning andcontrolling: consideration of the technological conditions when determining an optimal sequence of tasks..
(Quelle: GPM)
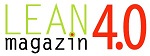
A steering committee is a decision-making body responsible for steering projects. In most cases, the steering committee is made up of managers from the organisational units involved in the project. Its tasks consist of controlling the reports of the project management, approving the project plan with all subplans, decisions on changes and acceptance of the project results. Other designations for steering committee are decision committee, steering committee.
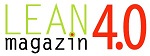
Supplier Kanban is based on the "Kanban"principle, but goes beyond the boundaries of the company and includes the suppliers in the principle. In contrast to Kanban, in supplier Kanban the point of consumption does not report its requirements to an internal supply point but to an external supplier. This supplier has the required products in stock. The goal of supplier Kanban is - as with Kanban - a demand-driven supply of parts, which is carried out by an external supplier. The determination of requirements is mainly carried out via Kanban containers, eKanban, transponder or RFID. Upon delivery and after an incoming inspection and booking, the parts flow directly into the internal Kanban system. Advantages of supplier Kanban:
-
Maximum delivery reliability for the supplier
-
Stocks and buffers are reduced
-
The replenishment time can be reduced to a few days or even hours due to high retrieval stability
-
Increasing our own flexibility and that of our suppliers
-
Cost reductions at the suppliers are possible
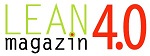
Life-Cycle means life cycle and is to be understood in marketing as product life cycle. In project management it is understood as the project cycle with the start of projects, typical project phases and the completion of projects. The further design of such phase models leads to process models.
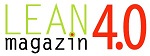
The value of a customer that can be generated by building a lifelong relationship. Can actually correlate with the age of the customer in business-to-customer transactions, but has different reference values in B2B (e.g. industry development).
(Quelle: Reinhold Rapp: Customer Relationship Management Campus 2000)
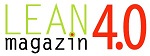
The LOB method is an instrument for planning and monitoring orders with small to medium quantities. It was designed by the US Navy in the fifties. The information for controlling the process is displayed graphically. Furthermore, the LOB method provides component-by-component information on the status of an order through all stages of production and procurement, depending on the planned completion dates of the end products. At certain points the LOB method compares the current status with the planning, so that deviations can be reacted to with corrective measures. Four elements make up this method:
-
For the production target, the quantities to be delivered as stated in the delivery schedule are clearly shown.
-
The production plan as the second element reflects the process of procurement, production, assembly and testing. It is illustrated by a numerical ray that ranges from the maximum time (left side) to the delivery of the final product at zero time (right side).
-
The production progress is recorded at the control points defined in the production plan and graphically represented by a histogram.
-
The last element of the method consists of the Line of Balance, which displays the target quantities at the defined control points at all times to ensure delivery times. For comparison, it is entered into the histogram of the production progress.
(Quelle: GPM)
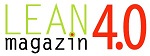
In the listing technique, the individual project parts are arranged in a list. The duration of the respective project part is shown. Depending on the project structure, start and finish dates are calculated and entered for the individual activities. The listing technique is mainly used for
-
Scheduling with few project parts
-
Linear processes without cross-linking
See also: GANTT Technology, PLANNET Technology.
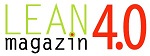
Bezeichnet eine Organisationsform, die nach Funktionen - wie z.B. Forschung und Entwicklung, Produktion, Vertrieb - gegliedert ist und bei der jeder Mitarbeiter fachlich sowie disziplinarisch einem Vorgesetzten zugeordnet ist. Eine Variante dieser Organisationsform bildet die Stab-Linien-Organisation. Hier erhalten spezialisierte Stabstellen fachliche Kompetenzen neben der Linie.
(Quelle: VDI Nachrichten Nr. 41)
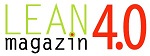
Physical guarantee of supply of the realisation processes with the allocated resources, including maintenance and disposal logistics.
(Quelle: GPM)
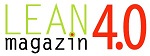
M
The time a machine takes to produce a unit, excluding loading and unloading.
(Quelle: TBM Consulting Group http://www.tbmcg.com/de/about/ terminology.php)
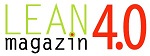
The Makigami process representation can be used to visualise and analyse business processes of any kind. This method is particularly suitable for eliminating losses in administrative procedures or in the office, where processes are generally less transparent. Each of the seven fatal losses for offices can and will be illustrated with the help of Makigami.
7 fatal losses for offices:
-
Defects (incorrect or incomplete information)
-
Waiting (for data, from other areas)
-
Verification (collecting signatures)
-
Post-processing (copying, changing)
-
Storage and stacking (file stacks, etc.)
-
Revise (search, non-unified procedures)
-
Moving (documents that are pushed around, illogical filing systems)
Makigami consists of three phases (in the form of answering the following questions)
-
How are we doing now? Analysis of the ACTUAL state! Visualisation of the current state.
-
What does our vision include? Development of the target condition/vision! Visualisation of the ideal state.
-
What is the first step towards our vision? Implementation plan to achieve the target state! Development of an improvement process.
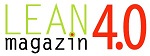
The authorisation of employees to interrupt the process in the event of malfunctions, thus preventing errors or standard deviations from being passed on to downstream processes.
(Quelle: TBM Consulting Group http://www.tbmcg.com/de/about/ terminology.php)
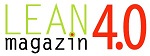
Material requirements planning is the temporal and quantitative determination of raw materials and components below the finished product level, which is necessary to carry out the production plan for finished products.
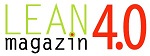
The mechanism is based on the explanation of phenomena exclusively through the analysis of the compelling cause-effect relation. Monocausal, deterministic and statistical thinking without consideration of feedbacks and interactions is the consequence.
(Quelle: GPM)
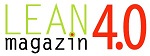
The term reusable logistics describes the use of plastic containers instead of one-way packaging (cardboard packaging) in internal and external transport as well as in the storage & commissioning of goods. The primary goal is the standardisation of packaging and the reduction of packaging waste. In contrast to the intralogistic implementation, the external management of such container pools is usually taken over by a pooling service provider, who returns, repairs, cleans, stores and feeds the containers back into the supply chain as required. The Lean Managementapproach, which aims to ensure the economic efficiency, processes and transparency of a returnable system, is called container management.
(Quelle: www.comepack.com)
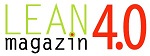
Milestones are events of special importance (definition according to DIN). The most important milestones in a phase model are the transitions from one project phase to the next.
(Quelle: GPM)
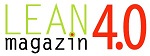
The Milestone trend analysis is a method for monitoring project deadlines. The prerequisite is a milestone plan in which the project is defined in individual milestones. The method works with estimated values which indicate the expected intermediate and final dates of the project. Fixed dates are assigned to each milestone and compliance with these dates is checked at periodic intervals. The estimated values are entered in the trend chart. This chart is constructed as a right-angled triangle: The vertical cathede represents the milestone dates, the horizontal cathede the reporting dates. Each estimated date of a milestone is listed at the respective reporting date and linked to the next one. This results in a curve in the chart for each milestone, which indicates the completion of the milestone as the hypothenuse of the chart is reached. If the curve rises, the end date of the milestone is delayed. If it remains relatively horizontal, the work is completed on time, if it falls, the milestone is completed sooner than expected. Deviations must be commented on, corrective actions should be indicated. The estimated values to be included in the trend chart can be determined by the employees (subjectively!) or by procedures such as the network technique ermittelt werden.
(Quelle: Mehrmann/ Wirtz, GPM)
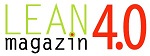
The completion value within a work package can be determined using the milestone technique if the work package lasts several months, if defined results (milestones) are available within the work package and if these can be assessed with costs. The completion value of the milestone is added to the previous completion value only after the milestone has been completed. An example: A work package with a total completion value of 200 is defined in three milestones with the values M1=50, M2=90 and M3=60. Two periods of completion are assumed for M1, one each for M2 and M3. After two periods M1 is completed, the completion value of the entire work package is 50. After period three M2 is completed with the value 90. The cumulative completion value is now 140 (=50+90). If the fourth period is closed with M3=60, the work package is completed and the cumulative earned value 200 (=50+90+60), and thus the final value, is reached.
(Quelle: GPM, Mehrmann/Wirtz)
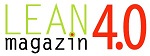
Under this method, the earned value is the ratio of a unit of measure to the planned total quantity. The unit of measure is valuated with the corresponding planned costs. This procedure requires that a time schedule is available that relates to parameters or quantities, and that measurable or countable results are achieved within the time frame of the work package (e.g. parts produced with the same value). The completion value is determined from the quantities already produced. If, for example, a work package consists of 50 units of quantity with an individual value of 10, the total value of the parts is 500. These units of quantity should be produced in three periods of 10, 15 and 25 parts respectively. After the first period, 10 parts are thus produced, the completion value is 100 (10 units of measure multiplied by the individual value 10). After the second period, 15 further units of measure are added to these 10 parts, so that the earned value increases to 250. The total value of 500 is reached when the last 25 units of measure have been completed and the work package is complete.
(Quelle: GPM, Mehrmann/Wirtz)
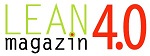
Mergers and Acquisitions is a collective term for the purchase or sale of company holdings, mergers or cooperations. It covers all activities in this field. In addition to business factors (financing, market and brand strategy), personnel-related factors make a significant contribution to the success of an M&A project. It is particularly important to prepare employees for working with their new colleagues by providing them with information about the other company and by working in mixed teams at an early stage and to encourage their commitment. The existence of an integration strategy, the involvement of HR management in the integration project group and the leadership of this project group by an experienced project manager with strong leadership skills are also significantly related to the overall success of an M&A project.
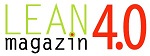
The essential and most frequently used component of many groupware systems. Dispatch of circulars by e-mail according to distribution lists; voice/video mail; internet conferences; internet protocols as a platform for group work: documents can be filed directly in the intranet without html knowledge or webmaster, so that different project groups can work with them at the same time.
(Quelle: Report Wissensmanagement: Wie deutsche Firmen ihr Wissen profitabel machen. Herausgeber: Prof. Dr. C.H. Antoni, Dr. Ing. T. Sommerlatte)
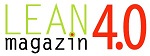
To work on a problem using the Metaplan method, the project manager needs good preparation and technical material. The procedure is that the project manager, as moderator of the meeting, presents the problem to his team by formulating important questions, writing them down in large letters on wrapping paper and pinning them to pin boards. The individual participants write their suggestions, approaches to solutions and opinions on the respective topic on colourful cards, which are sorted according to importance and arranged on the pin boards. The metaplan technique thus gives the opportunity to present problems in a structured way. At the end of a session it should be clear to each participant how the problem is to be solved and which functions and tasks are assigned to him. To this end, the project manager must summarise the results and make them available to every member of the team (e.g. by photographing the finished pinboards and handing out photocopies). It may be necessary to distribute homework and arrange another meeting.
(Quelle: Mehrmann/Wirtz)
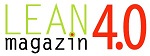
With this method of determining the completion value, the Work package is assigned a value of 0 at the beginning and during its execution. Only from the moment of completion is it valued at 100%. The work package must therefore lie within a reporting period (e.g. one month).
(Quelle: GPM)
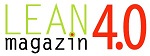
If the duration of a work package is no more than three months and detailed planning is not possible, the 50-50 technique is the best option. The determination of the completion value is distorted by the fact that 50% of the completion value is credited to the work package at the beginning and 50% at the end without taking the interim development into account.
(Quelle: Mehrmann/Wirtz, GPM)
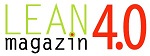
The Metra Potential Method (MPM) is a network techniquedeveloped by the French company SEMA in 1958. It is designed as an activity node network (VKN) and works like "CPM" with a deterministic time model.
(Quelle: Mehrmann/Wirtz)
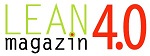
The method of mind-mapping combines linguistic and pictorial thinking. In the middle of a large sheet of paper, the subject to be worked on is written down, from which the thoughts of the individual person or group now develop. The thoughts are presented graphically according to their importance as main branches with secondary branches growing out of the centre. For clarity, the branches can be identified by colours. This method of making notes can be extended at will and is extremely variable.
(Quelle: Mehrmann/Wirtz)
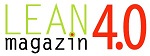
The time during which a person carries out a specific work process, including times for loading and unloading parts, excluding waiting times.
(Quelle: TBM Consulting Group http://www.tbmcg.com/de/about/ terminology.php)
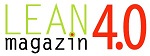
Project management consists of the following modules:
-
Planning
-
Guided tour
-
Control system
-
Structural organisation
-
Process organization
-
Project goals
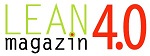
This specified form informs the client / the decision-making body about the current status of the project and its progress, unscheduled changes and any special features that have occurred that have an influence on the course of the project. The month or quarter can be agreed as the reporting period.
(Quelle: GPM)
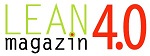
The task of the monitor group is to prepare the expert rounds of the survey according to the Delphi-Method select the experts, assign the questionnaires and evaluate them.
(Quelle: Gabler Management)
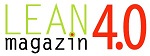
This analytical method or structured research was developed by Prof. Fritz Zwicky from the TU California. It describes the most important parameters and their variables of a problem and arranges them in a coordination system. In a problem that has 2 important performance parameters, the shape of the matrix would be a rectangle, for 3 parameters a cube. Such a model is called a card index box with drawers. Each drawer is filled with a variant of e.g. 3 parameters. Some of these drawers are quickly filled with existing concepts. A large number of drawers, however, are empty, often because nobody has thought of combining the possible variants in this way.
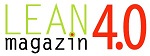
The Morphological Box attempts to present theoretically conceivable solutions to a particular problem. In doing so, the problem is broken down into its essential but independent features. These are arranged in a box and individual possibilities are tried to be found. The individual possibilities for these characteristics are noted down as analytical working aids. Finally, the characteristic values are combined so that new approaches to solving the problem are found.
(Quelle: Mehrmann/Wirtz)
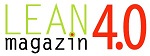
Japanese for wastefulness. Any activity that consumes resources without directly contributing to the added value of the product.
(Quelle: TBM Consulting Group http://www.tbmcg.com/de/about/ terminology.php)
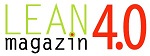
This method of situation analysis makes use of random short-term observations in order to obtain statistically reliable results on quantity and time data. If it is a quantity survey, it is called a multi-moment frequency method (MMH); if the subject of the investigation is time recording, the term multi-moment time measurement method (MMZ) is used. With careful preparation, the multimoment recording should take place in the following steps:
-
Preparation of the affected operational areas for the investigation Demarcation and concretisation of the object of investigation
-
definition of observation elements (e.g. types of communication, activities during operation)
-
Development of an observation schedule in time intervals (random time table helpful)
-
Determination of the order of the shooting situation per tour (strict adherence to this order during the entire duration of the recording)
-
Preparation of recording lists for recording mathematical-statistical data evaluation
(Quelle: GPM)
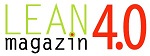
See quantity proportionality
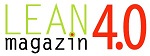
Coordination of deadlines and use of resources between several projects in order to develop synergy effects and avoid mutual interference.
(Quelle: GPM)
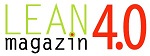
deviations from the standard values of process quality, costs and delivery dates.
(Quelle: TBM Consulting Group http://www.tbmcg.com/de/about/ terminology.php)
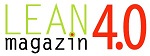
Exaggeration and congestion: demand overwhelms capacity.
(Quelle: TBM Consulting Group http://www.tbmcg.de/resource-center/lean-sigma-glossary-terms.html#letter-m)
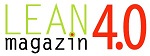
N
See Claim-Management
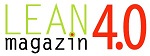
Perform two or more activities in one movement.
(Quelle: TBM Consulting Group http://www.tbmcg.com/de/about/ terminology.php)
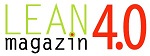
A network update is the recalculation of the network on an update date taking into account the feedback received.
(Quelle: GPM)
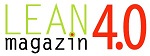
Definition of network planning technology according to DIN 69 900: All procedures for the analysis, description, planning and control of processes on the basis of graph theory, whereby time, costs, resources and other influencing variables can be taken into account.
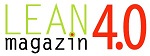
A network summarisation is the reduction of the number of activities, events or relationships in a network without changing the project flow structure (definition according to DIN). This procedure is appropriate if a detailed network plan, which in practice is often already created from the descriptions of the work packages, is to be developed into a rough or outline network plan which does not yet exist.
(Quelle: GPM)
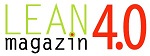
See subnetwork technology
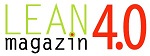
Any activity that increases costs without adding value to the product or process.
(Quelle: TBM Consulting Group http://www.tbmcg.com/de/about/ terminology.php)
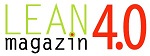
A method of production planning that ensures that fluctuations in customer demand over a given period of time do not affect production. Each part is produced every day.
(Quelle: TBM Consulting Group http://www.tbmcg.com/de/about/ terminology.php)
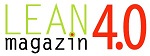
Any activity that increases costs without adding value to the product or process.
(Quelle: TBM Consulting Group http://www.tbmcg.com/de/about/ terminology.php)
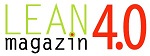
Hoshin-Kanri Hoshin-Kanri contains a target hierarchy. The multi-annual goal (Ideal or Vision) is the North Star (True North), on which the annual goals, but also the concrete improvement activities are based. Because the North Star is aligned with customer needs, the previously different and sometimes contradictory management objectives can be redefined, synchronised and aligned with each other. This resolves some of the previous conflicting objectives.
(Quelle: http://www.wandelweb.de/wiki/index.php5?title=Hoshin_Kanri)
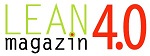
Normal sequence: This term from the network technique describes the usual arrangement of activities within a network. The start of an activity is dependent on the end of its predecessor(s), i.e. the activity in question cannot be started until the predecessors have been completed.
(Quelle: GPM)
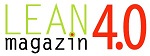
The utility value analysis (NWA) is a method of demonstrating the benefits that cannot be measured in monetary terms. It is carried out in several sub-steps: First, the team collects all the key objectives of the investment that cannot be quantified in monetary terms, including in a deductive and intuitive way. Then the weighting of the objectives is carried out, giving relative importance to each objective (various procedures are possible), with the system of objectives always being weighted from top to bottom. As a third step, value standards are now set up which later make it possible to assign degrees of fulfilment to the individual alternative solutions of the objectives. The degree of fulfilment indicates the extent to which the specified objective is achieved. The team then draws up an evaluation table of the alternatives, which only assigns a step weighting to the objectives in the lowest category. The subsequent calculation of the utility values is carried out by multiplying the weight and evaluation. The total utility value of an alternative is obtained from the sum of all relevant utility values. If there are several solution alternatives, they are listed hierarchically according to their total utility values. The sensitivity analysis is only carried out if there is doubt about the correctness or accuracy of the results and if the total utility values of the best alternatives are close together. As a final step, each individual result is presented and assessed to justify the decision.
(Quelle: GPM)
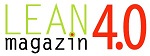
O
This mixed form of presentation of a work breakdown structure, which partly takes into account the object-oriented and partly the function-oriented structure, has proven itself in practice, as it largely corresponds to both structural forms. See also: Work breakdown structure (WBS)
(Quelle: GPM)
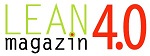
In this possible form of a work breakdown structure , the project object is subdivided into subsystems and subsystems, main assemblies, subassemblies, etc. according to a system classification. The object-oriented structure is also called result- or product-oriented structure. See also: Work breakdown structure (WBS)
(Quelle: GPM)
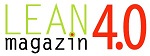
The commitments that project officers make to external contractors (e.g. when ordering materials) for their work are called commitments. These commitments are to be paid during order processing or after completion of the order. The cost planning must be completed by a planning of payment obligations. Actual costs and commitment reflect the total consumption of a project up to its cut-off date.
(Quelle: GPM)
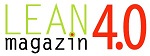
A production concept in which only one part at a time moves from one workstation to the next, without the possibility of stocks forming in between.
(Quelle: TBM Consulting Group http://www.tbmcg.com/de/about/ terminology.php)
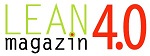
Individual communication with the customer, e.g. personalised dialogue via direct mailing or Internet/e-mail
(Quelle: Reinhold Rapp: Customer Relationship Management Campus 2000)
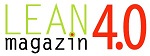
Even more comprehensive than one-to-one communication. Personalised marketing measures with individual distribution, product management and pricing.
(Quelle: Reinhold Rapp: Customer Relationship Management Campus 2000)
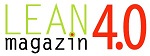
The reduction of makeready work to a single work step.
(Quelle: TBM Consulting Group http://www.tbmcg.com/de/about/ terminology.php)
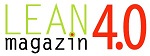
Die Zeit, in der eine Person einen bestimmten Arbeitsablauf ausführt, einschließlich der Zeiten zum Laden und Entladen von Teilen, ausschließlich der Wartezeiten.
(Quelle: TBM Consulting Group http://www.tbmcg.com/de/about/ terminology.php)
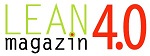
The optimistic network plan update works on the principle:
No feedback = work progress according to plan.
Postponements are avoided by adjusting the percentage of completion of activities or resource allocations accordingly before recalculation. Activities are reported as completed if their finish date falls before the update date.
(Quelle: GPM)
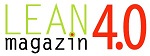
This graphic representation of the formally regulated relationship and competence structure within an organisation does not illustrate the functional interrelationship of work processes or the degree of cooperation, but only gives an overview of the rough structure of the multi-level superiority and subordination as well as the structure of the various departments and functional areas in the company.
(Quelle: Schneider/Lexikon zu Team und Teamarbeit)
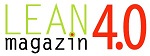
Structural and process organisation in the project, their adaptation to the project progress and integration into the supporting organisation.
(Quelle: GPM)
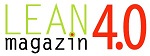
Ein Organisationsprojekt soll Aufbau- und/oder Ablaufstrukturen in Organisationseinheiten neu schaffen bzw. verändern. Die betroffenen Strukturen sind immaterieller Art und zunächst von den materiellen Beschaffungen und Veränderungen zu trennen. Inhaltliches Projektziel ist damit ein neuer oder veränderter Zustand einer Teilmenge menschlicher Individuen. Ist dieser Zustand erreicht, kann das Projekt als abgeschlossen gelten. Die Umorganisation eines Betriebes oder die Einführung von Bürokommunikation etc. werden dieser Projektart zugeordnet.
(Quelle: Mehrmann/Wirtz, GPM)
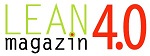
Also known as active telemarketing, this means targeted calls to groups of addressees. The customers of the commissioning company are called by the call centre, the call agents report under the company name of the commissioning company. Typical outbound services include arranging appointments, address qualification, determining decision-makers, welcoming new customers, mailing follow-up etc.
(Quelle: Reinhold Rapp: Customer Relationship Management Campus 2000)
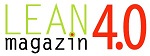
The term Overall Equipment Effectiveness (GAE) is a key figure developed by the Japan Institute of Plant Maintenance. It is one of the results of decades of development of the TPM concept (Total Productive Maintenance). Overall Equipment Effectiveness is a measure of the added value of a plant. The GAE of a plant is defined as the product of the following three factor:
-
Availability factor
-
Power factor
-
Quality factor
Their value range is between 0 and 1 or between 0 % and 100 %. World-class companies achieve an OEE of 85% from an operational perspective in the manufacturing industry and 95% in the process industry from an operational perspective. GAE is defined as product of availability factor, performance factor and quality factor. Thus follows:
GAE = availability factor x power factor x quality factor
The result is a percentage value that indicates the proportion of the planned machine running time that has actually been produced. This value is usually well below 100%, since the factors involved are also usually below 100%. In this way, a wide variety of wastes are made clear. The benefit of GAE consists in the reliable analysis of machine time losses, exact calculations and evaluation possibilities, consideration of interfaces and interdependencies and thus lets the management look at the plants with a different view.
(Quelle: Wikipedia.de)
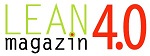
P
A technology with which a process is adjusted to the cycle time.
(Quelle: TBM Consulting Group http://www.tbmcg.com/de/about/ terminology.php)
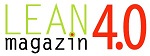
Ensuring project teams composed according to professional and social competence, their effective project work and reintegration after project completion.
(Quelle GPM)
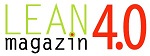
The pessimistic update of a network plan is based on the formula:
No feedback = no work progress.
Prior to recalculation, the confirmation dates of all processes that have been started are moved to the update date, while the percentage of completion remains unchanged. All open tasks are moved after the update date. Unnecessary postponements occur if an activity has been processed but not confirmed for a long time.
(Quelle: GPM)
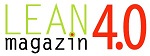
The specification sheet
-
is the collection of the requirements for the project
-
is structured
-
is complete or defined missing components
-
will be progressively detailed
-
is consistent
-
is developed by the client + the project
-
is formally the responsibility of the project manager
-
is known to all parties involved
-
is regularly reviewed (milestones) and adjusted if necessary.
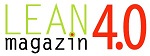
The result protocol of the phase acceptance meeting is called phase acceptance report. It documents the review of the completed phase with an overview of the phase results and statements on the compliance with the phase objectives. It also includes the release of the subsequent phase. This report, for which a specified form is used, must be signed by the decision authority/client.
(Quelle: GPM)
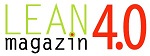
If a transition from one project phase to the next is imminent, a phase decision meeting is held to collect the results of the completed phase and to initiate the follow-up phase. This meeting is usually a Milestone at which a decision is made on whether to continue the project, repeat a phase or abandon the project.
(Quelle: GPM)
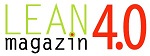
A phase model is the representation of a project process divided into time sections, each of which can be clearly identified and which provide an essential partial result of the overall project.
(Quelle: Mehrmann/Wirtz)
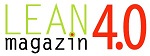
Pitch defines the time interval in which work on the pacemaker process is released and finished products are removed. As a rule, an attempt is made to design the time interval according to the container size for finished products. The pitch can also be understood as a management time frame, which allows a target/actual comparison of the output. To support the pitch, compensation boxes, also called "Heijunka boxes", are suitable, in which "Kanban" -cards specify the product sequence for the pitch increments.
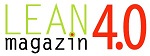
Data collection and processing in predefined Excel sheets (PFEP)
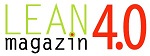
Planning means looking ahead, mentally developing a future model with the help of analysis, whose means of implementation are optimally matched to the model requirements, so that a feasible, logical implementation concept is created.
(Quelle: GPM)
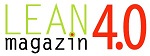
The PLANNET technology (Planning Network) is a further development of the GANTT TechnologyIt attempts to incorporate the essential disadvantage of the GANTT technology, namely that the scheduling dependencies are not recognisable, graphically into this technology. This is done by using connecting lines to represent the scheduling dependencies. This automatically results in the display of buffer times. These times are shown as dashed lines. The PLANNET-technique is often used for project scheduling for a few project parts Requirement of a visually convincing form of presentation Graphical representation of dependencies and buffer times.
See also: Listing technology.
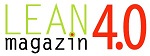
Planning boards support the visual presentation of projects, tasks or processes in their sequence and with their time and capacity requirements. This enables quick recognition of availability, responsibility, capacity utilisation, the status of processing or impending delays in deadlines and thus an immediate reaction. The task definition determines the type of planning. Fields of application for planning boards are:
-
Personnel Planning
-
Order planning
-
production planning - "Kanban" Control system - CIP blackboard - Heijunka Board
-
Workshop planner
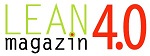
The planning meeting takes place at the end of a project phase and is often combined with the phase decision meeting. It serves to revise, improve and detail the rough planning of the subsequent phase on the basis of the findings and results from the preliminary phase.
(Quelle: GPM)
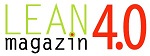
An improvement that is limited to a specific workstation and quickly carried out by two or three experts. Usually follows a Kaizen workshop.
(Quelle: TBM Consulting Group http://www.tbmcg.com/de/about/terminology.php)
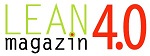
apanese for "error avoidance". A Poka-Yoke device prevents a human error from interfering with the machine work or process and eventually degenerating into a product defect.
(Quelle: TBM Consulting Group http://www.tbmcg.com/de/about/terminology.php)
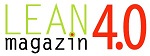
Concept in which the strategic business objectives of a company are aligned with the available resources and communicated at all hierarchical levels in order to bind all employees to these common objectives.
(Quelle: TBM Consulting Group http://www.tbmcg.com/de/about/ terminology.php)
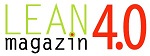
One speaks of a portfolio procedure when business units of a company (e.g. products, sources of capital, employees, projects, etc.) are strategically positioned so that its short-term success and long-term existence are optimised. A two-dimensional diagram is used for graphical representation. On its horizontal axis the current position of the business units under consideration (e.g. market share of products) is shown. The vertical axis contains the future attractiveness of the business units (e.g. growth of product markets). A development path (e.g. project phases, project life cycle), which the business units follow, is included in the diagram. A project portfolio decision starts with the operationalisation of the current situation of projects (e.g. efficiency, effectiveness) and their attractiveness (e.g. expected order volume). After measuring their characteristics, the project data are entered into the diagram. On the basis of the diagram, it is now possible to read off the economics of each individual project and make strategic decisions.
(Quelle: Gabler Management)
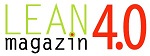
A table which is mainly used when working with machines and compares the workload of the machine with its capacities.
(Quelle: TBM Consulting Group http://www.tbmcg.com/de/about/ terminology.php)
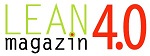
A method of production planning that ensures that fluctuations in customer demand over a period of time do not affect production.
(Quelle: TBM Consulting Group http://www.tbmcg.com/de/about/ terminology.php)
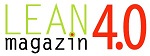
A method of production planning that ensures that fluctuations in customer demand over a period of time do not affect production.
(Quelle: TBM Consulting Group http://www.tbmcg.com/de/about/ terminology.php)
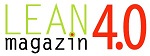
Productive creativity reflects the ability to copy. It is realistic, objective and complete. However, the product produced does not show any significant differences from the original product.
See also: Expressive Creativity
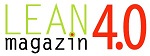
Product quality means making the required functionality available, including the necessary implementation support (e.g. operating manuals).
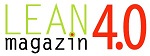
In the Program Evaluation and Review Technique (PERT) an optimistic, a probable and a pessimistic time estimate is given for each process. This network method is designed as an Event Node Network (EKN) and was developed in 1958 by the US Navy together with the companies Boots & Hamilton and Lockhead.
(Quelle: Mehrmann/ Wirtz)
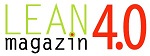
This calculation for determining the date serves to determine the earliest possible date. All project events required prior to the event in question must be included in the calculation. Thus the calculation starts at the beginning of the project, i.e. at the start events or processes.
(Quelle: GPM)
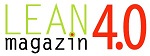
The starting point for progressive (forward) scheduling is the beginning of the project. This date can be directly after the project planning. However, it can also be set at a later date due to circumstances that are independent of the project. From the beginning of the project, the project is then scheduled forwards into the future. The final result of this calculation is the project end date.
See also: Retrograde scheduling.
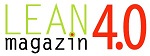
Project Office is a central service point in the company, which provides relief and support for the individual projects. Tasks can include some or all of the following service functions:
-
Completion of administrative day-to-day work for individual projects (paperwork, coordination of deadlines)
-
Development and provision of organisational regulations and standards for project work
-
Carrying out controlling tasks (helping to define project objectives, reducing the number of simultaneous projects, coordinating project teams, project prioritisation)
-
Planning of personnel development measures for project members
-
Coaching of project managers
(Quelle: GPM 2/00)
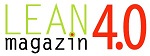
A project is a project which is essentially characterised by unique conditions in its entirety, such as
-
Target
-
Time, financial, personnel or other limitations
-
Distinction from other projects
-
Project specific organisation
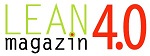
The final project report presents the results of the overall project from an organisational and technical point of view. It also presents the new findings for future projects are detained. The report deals with the project execution (initial situation, major events, schedule, expenditure/cost overview, deviation analysis, consequences and experiences) and the project content (objectives, procedure, results, recommendations).
(Quelle: GPM)
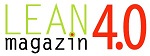
Procedure for the initialisation of projects.
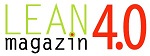
Project types are not differentiated by the criteria of their size or complexity etc., but by their content. In this way, a distinction is made between investment projects, organisational projects and research and development projects.
(Quelle: Mehrmann/Wirtz)
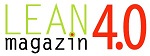
The project order forms the basis for the project team at the beginning of a project. It is based on a contract concluded with the client and the preceding offer with the agreements specified therein, such as scope of services, deadlines and expenditure. The standards, methods and guidelines to be observed, e.g. obligations of the client, agreements on project handover, quality criteria, rules for project control, etc. must be laid down.
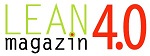
Project budget is the total sum of the planned costs available to the project manager for the implementation of the project. The budget is estimated and calculated during the planning phase on the basis of the work packages. The budget can either be provided as one sum or paid out successively according to the progress of the project (e.g. after reaching (milestones).
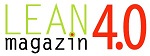
This collective term stands for the overall project management, which is made up of the project manager and his closest colleagues (lawyers, engineers etc.). As they form an integrated team, they should be housed in a common office complex.
(Quelle: Madauss: Projektmanagement)
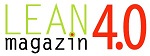
Project controlling serves the early recognition of deviations in projects. Planned and actual results are compared to determine the status. The project report of the project manager serves to assess the deviations. Project controlling is increasingly being performed by staff units that monitor several projects and perform overarching project coordination tasks.
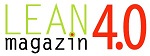
The end of the project is reached when the last phase results have been accepted.
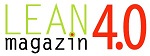
Project approval is a formal act by the decision makers to implement a project. The project approval can take place in stages. For this purpose, a preliminary study is first released, after whose evaluation the project order is released.
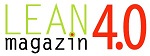
The project discussion is an important instrument of communicative leadership. It serves to better prepare the project participants for their project assignment, to ensure the quality of work, to increase the efficiency of the work and to ensure the growth of know-how.
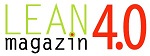
A project group meets the same requirements as a team; however, a team does not have a hierarchical structure; a group is always headed by a group leader.
(Quelle: Mehrmann/Wirtz)
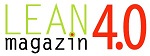
Project initialisation is the first phase of a projec t. The result of this phase is a written project assignment agreed with all persons and organisational units concerned. This contains the concrete project objective and defines the framework conditions under which the project is to be carried out.
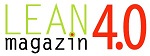
Project indicators are numerical values of parameters used as a benchmark for technical or economic relationships. They are an important tool of the controlling however, they bear risks in that they relativise and thus distort reality. Often these figures are mean values which show a very wide spread.
(Quelle: GPM)
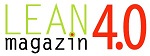
The individual costs are either grouped together in homogeneous cost categories or divided into further sub-categories (definition according to DIN 69903). The cost types are differentiated according to their origin, such as energy costs, production wages, rents, etc. If too many cost elements are included in the planning, their expenditure becomes unnecessarily high, so that it is advisable to create groups of cost elements, e.g. turning, milling and grinding work to be classified in the category production work.
(Quelle: GPM)
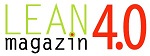
DIN definition: The project cost unit is a project result or partial result to which project costs are allocated according to the polluter-pays principle.
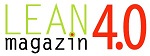
A project crisis is a normal, cyclically recurring state of uncertainty in demanding projects. Primarily caused by project teamdecision-making body or rumour mill. By project control techniques, calm and strong nerves usually quickly remedied.
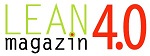
As an independent social system, a project has a culture. Therefore, all values, norms and rules of a project can be summarised under the term project culture. The development of a project culture takes a long time, which has to be compensated by a high expenditure of energy, as the project itself is time-bound. For the members of a team, the examination of the project culture can be an orientation aid and contribute to their identification with the project.
(Quelle: GPM)
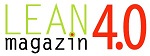
According to DIN 69 901, project management means: the totality of management tasks, organisation, techniques and means for the execution of a project.
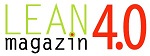
In contrast to normal tasks, projects have certain characteristics. projects are:
-
TARGETED i.e. the services to be provided in the context of a project must be described in detail in advance of a project.
-
EXCLUSIVE, i.e. the scope of the project is limited in terms of time, performance and costs - start and end dates are fixed.
-
SUPER-GLOBAL, i.e. in the company different departments, groups or functional areas are involved in a project. The Project goal must serve a corporate benefit.
-
UNSCHEDULED, i.e. the task to be solved in the project is outside the operational routine (no maintenance work) and cannot be solved by the line organisation alone
-
COMPLEX, i.e. the task is complex in scope or nature. Many boundary conditions have to be considered and converted into different solutions.
-
SIGNIFICANT i.e. a project, depending on its size, is associated with significant costs and risks for a company.
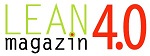
The projects that a company runs at the same time and their relations to each other can be perceived as a project network. Project networks are networks of relatively autonomous projects that are loosely or closely linked.
(Quelle: GPM)
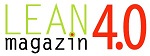
Project organisation refers to the organisation charged with the implementation of a project and its integration into the existing company organisation. It is in contrast to the Line organization.
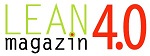
Definition according to DIN: A project phase is a temporal section of a project process that is objectively separated from other sections.
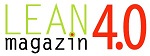
Project planning is a tool for achieving the agreed Project goal It serves as a benchmark for objective progress control and as a basis for project management. Project planning can be supported by project management -tools.
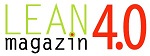
See project controlling
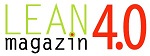
The project structure level is a branch of the work breakdown structure which shows the subtasks and work packages to be solved at this point.
See also: Work breakdown structure (PSP), Subtask (TA), Work package (AP).
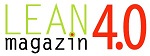
Definition according to DIN: A work breakdown structure is the representation of the project structure. It can be presented according to the structure, the sequence of events, basic conditions or other aspects, e.g. mixed forms.
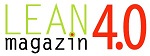
Project responsibility is divided among the committees of the project organisation he project manager has the following responsibilities:
-
Organisation, planning, management and control of the projects
-
Technical leadership of the team
-
Creating the conditions for the implementation of the Project goals
-
Achievement of the project objectives Communication with all bodies involved in/affected by the project
-
Assessment of the team members in the context of the project work
-
Information of the team members and the responsible bodies and committees
-
Project post-calculation
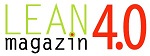
A project objective is an anticipated state which is consciously chosen and desired and is achieved through active action. The project goal must be understood and supported by all project participants. All activities of the project work are exclusively geared to the project goal. Incorrectly understood, hidden or unspoken project goals can have a lasting negative impact on project success or prevent it altogether. The project objective does not describe the solution. The project objective does not describe the solution.
Project objectives are clear, acceptable, feasible, positive, understandable, consistent, qualified, complete, up-to-date, meaningful, prioritised.
Definition according to DIN: The project objective is a verifiable result and specified realisation conditions of the overall task of the project.
See also: Target dates, Strategic objectives, Cost targets.
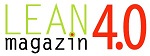
The results of all meetings (status, planning and technical meetings), which regulate the internal company determination of project activities and the determination of the distribution and monitoring of tasks, are recorded in minutes. These are included as documents in the project documentation.
(Quelle: GPM)
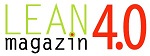
For many complex and innovative projects it is advisable to develop prototypes. This process is called prototyping. In this process, an example system is designed which shows the essential characteristics of the later end product. However, this procedure cannot replace the conventional phase concepts, but provides the manufacturer with additional advantages, such as early error detection, clear presentation, etc. A distinction is made between expansion prototyping and disposable prototyping, furthermore functional prototypes and explorative prototyping.
(Quelle: Mehrmann/Wirtz)
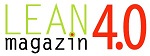
A process is the content-related, chronological and logical sequence of activities.
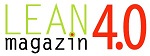
A table which is mainly used when working with machines and compares the workload of the machine with its capacities.
(Quelle: TBM Consulting Group http://www.tbmcg.com/de/about/terminology.php)
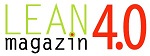
The members of a pseudo-team are not seriously interested in practicing a common approach, defining a purpose for the group's existence, setting work priorities, and striving for a common performance goal. The advantages of teamwork are deliberately neglected, so that the actual concept of team does not apply to such a working group.
(Quelle: Schneider: Lexikon zu Team und Teamarbeit)
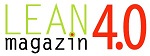
Definition of buffer time according to DIN 69 900 Buffer time is the period of time by which the position of an activity can be changed without affecting the project duration.
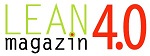
Q
Totality of the cross-element general measures and regulations for ensuring and demonstrating the quality of products and processes.
See also: Six Sigma.
(Quelle: GPM)
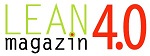
Single Minute Exchange of Dies (SMED) or QCO (Quick Change Over) is a process designed to reduce the set-up time of a production machine or production line. The aim is to reduce inventories by converting the machine to a new production process without disrupting the production flow, or to increase the flexibility of machines, lines and processes using a proven method. Video analyses, time analyses, work standards are used for this purpose. In several iterative steps the set-up time is first improved by organisational and later by technical measures. To minimise costs it is important that the steps are carried out in the specified order. The process is carried out in 4 (5) steps:
-
separation of internal and external set-up processes (organisation)
-
Conversion from internal to external set-up processes
-
Optimisation and standardisation of internal and external set-up processes
-
Elimination of adjustment procedures
-
(parallelisation of set-up processes)
Various techniques are used for optimisation, such as
-
Preparation of the production changeover
-
Use of clamps instead of screws
-
Sliding tables instead of cranes
-
separate preheating
-
intermediate clamping devices for adjustment outside the machine
-
Parallel set-up processes "simultaneously instead of consecutively", i.e. using several employees instead of one (often regarded as a fifth step)
-
Elimination of adjustments
-
Mechanisation Standardisation of set-up activities
-
Standardisation of tool dimensions
(Quelle: wikipedia.de)
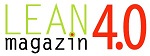
R
Definition according to DIN 69900: A framework network plan is a roughly worked out overall network plan of a projec t, which describes the framework for the process structure as well as for the time, cost and/or resource planning of the entire project, if necessary for the individual phases of the project process.
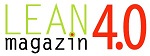
This technique for task classification according to Jordt/Gscheidle provides for structuring the recorded data on a grid sheet and displaying it as a classification tree. This method is flexible and easy to use, as it can be applied at the respondent's workplace, at the organiser's workplace and when developing structures.
(Quelle: Mehrmann/Wirtz)
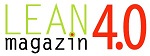
The (ontological) reductionism as a principle of thought in science and technology is based on the conviction that everything must merely be broken down into its parts in order to be able to understand, classify and evaluate the whole from the analysis of the parts.
(Quelle: GPM)
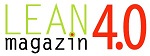
The formal definition of reengineering is: Fundamental rethinking and radical redesign of essential business processes in companies or parts of companies. The results are significant improvements in important and measurable performance indicators in the areas:
-
costs
-
quality
-
service
-
time
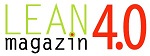
Association for Work Studies and Company Organisation
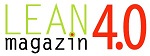
This technique is used for work packagesthat have a dependency on other work packages. The work value of the dependent packages is defined as a fixed ratio to the value of the higher-level work packages calculated by another method (e.g. the Milestone method). In practice, this method is suitable e.g. for design reviews, for tests of produced pieces etc.
(Quelle: Mehrmann/Wirtz)
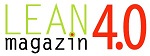
The latest possible date is determined by the retrograde invoice. In doing so, it is important to take into account all project events that are necessary after the respective event until the end of the project. This calculation therefore starts at the end of the project, i.e. at the target events or activities.
(Quelle: GPM)
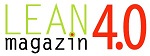
Retrograde (backward) scheduling is applied when the end of the project is predetermined. From the end of the project, scheduling is then backwards towards the present. It can happen that the start of the project lies in the past. By changing scheduling requirements, such as reducing the time required for a project part or planning the deployment of additional project staff, a new scheduling can achieve an improved result.
See also: Progressive termination.
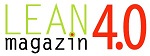
This is a method of time planning in which the interim results achieved form the basis for new sub-projects to be started, while the sub-project delivering interim results continues on its own. This form of planning process is suitable for development projects that have highly ramified dependencies and in which sub-projects may well die.
(Quelle: GPM)
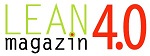
The risk analysis must identify, evaluate and prevent possible dangers for the Project Furthermore, risk factors must be identified, analysed, evaluated and countermeasures taken.
(Quelle: GPM)
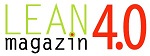
The risk assessment must quantify the risks identified in the risk analysis in monetary units and evaluate them according to their probability of occurrence. The expert survey is suitable for this purpose. Since the effort of an expert survey is too great for small projects, the costs must be determined with the help of the individual risks and their probability of occurrence. The product of these two values results in the probable costs for each individual risk factor. The sum of the probable costs of all individual risks gives the total risk provision required.
(Quelle: GPM)
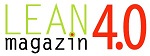
The risk documentation as the second and final stage of risk analysis is used to detail the identified risks. It is important to determine how the risks can be placed in the expected time frame (tool: process planning), what effects a risk has on other work packages, what causes can cause the risk to occur, and finally what preventive or corrective measures must be taken.
(Quelle: GPM)
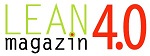
This first step of the risk analysis to identify the risks for the project. A useful tool is the work breakdown structure, which is used to check all work packages for possible risks. A distinction can be made between factual (technical), scheduling and financial risks. In this way, a list of expected risks and their assignment to the respective Work package.
(Quelle: GPM)
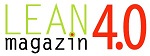
Securing the projects by recording and assessing as many risks as possible, and managing them by taking measures to avoid, insure, mitigate or pass them on
(Quelle: GPM)
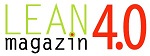
The risk selection process identifies the risks that have the maximum impact on the risk situation of the project. Suitable for this purpose is the ABC-Analysis.
(Quelle: GPM)
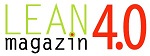
Rationalisation Board of Trustees of the German Economy e.V.
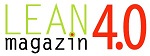
S
-
Was soll geliefert werden?
-
Welche Funktionen sollen erfüllt werden?
See also: Project goal, Strategic objectives, Cost targets.
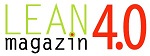
Processes, software and tools to support and automate the sales process. SFA includes, for example, contact management, forecasting and sales administration.
(Quelle: Reinhold Rapp: Customer Relationship Management Campus 2000)
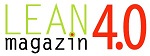
Production of a product with a minimum use of resources (labour, materials, capital, machinery, etc.) and in compliance with the delivery date.
(Quelle: TBM Consulting Group http://www.tbmcg.com/de/about/terminology.php)
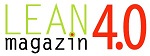
Barriers are limit values that must not be exceeded or undercut. They determine, for example, how many resources are intended for a particular Work package Limits are also set for project time and costs.
(Quelle: GPM)
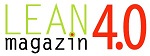
A technique by which a process is adjusted to the Cycle time .
(Quelle: TBM Consulting Group http://www.tbmcg.com/de/about/terminology.php)
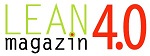
Scrum is a lean framework for project management and is assigned to the so-called agile methods. Scrum is characterised by iterative-incremental work with deliveries in short intervals, early customer feedback, simple and clear rules, exactly three roles, strict adherence to time limits (so-called time-box) for iterations and meetings as well as a strong focus on quality and efficiency. Added to this is the effort to avoid waste. The basis of the work is a clearly prioritised list of requirements according to business value, the so-called product backlog. A self-organising, mostly interdisciplinary team with equal members works through this backlog maintained by the so-called Product Owner and strives to have as little WIP (Work in Progress) as possible at all times. Instead, as a team, requirements are worked through one after the other as far as possible in order to minimise risk, protect the client's investment and achieve a quick amortisation of the capital invested. Team and product owner are supported by a moderator responsible for the Scrum process, the so-called Scrum Master. Scrum is mainly used in software or IT projects, often combined with practices from the so-called XP (Extreme Programming), but is basically applicable across industries and technologies, which is often the case. Scrum is also used at the management level to control entire companies (divisions). The framework also offers the possibility to scale with little overhead to large (multi-)projects with several teams or value streams.
(Quelle: Alexander Kriegisch, Scrum-Master.de)
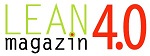
See relational method.
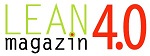
A respectable master or teacher.
(Quelle: TBM Consulting Group http://www.tbmcg.com/de/about/terminology.php)
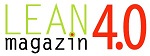
Processes, software and tools to support and automate the sales process. SFA includes, for example, contact management, forecasting and sales administration.
(Quelle: Reinhold Rapp: Customer Relationship Management Campus 2000)
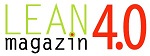
-
Dirty - schmutzig
-
Dangerous - gefährlich
-
Difficulte - schwierig
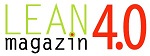
Shop floor management (SFM) is a management tool for all levels of the company. It enables:
-
Highlighting the current conditions at the place of value creation
-
Detection of deviations from the defined target state
-
Sustainable problem solving
The linchpin of shop floor management is the so-called SFM board. At regular intervals, cross-hierarchical board meetings take place on the following topics:
-
Staff allocation: Quick overview of staff and thus optimised use of resources. Bottlenecks and overhangs become immediately visible.
-
Job control: Every employee present has assigned jobs based on the available job volume.
-
Standards-based process control: Recurring management tasks are visualised. Compliance with defined standards (e.g. occupational safety, cleanliness and order) is ensured by on-site process controls. These process controls serve on the one hand to prevent errors and on the other hand as a source of possible optimisation measures
-
Key figures: By means of deviations from the target value, weak points can be identified and a problem-solving process can be initiated immediately.
-
Problem-solving process: The modules described above ultimately serve to quickly identify deviations. The structured problem-solving process serves to restore the target state.
These board appointments are part of an interdepartmental communication structure and form the framework for structured daily routines. Books: Shopfloor Management
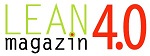
Shopfloormanagement (kurz SFM) ist ein Führungsinstrument über alle Ebenen im Unternehmen. Es ermöglicht:
-
Highlighting the current conditions at the place of value creation
-
Detection of deviations from the defined target state
-
Nachhaltige Behebung von Problemen
The linchpin of shop floor management is the so-called SFM board. At regular intervals, cross-hierarchical board meetings take place on the following topics:
-
Mitarbeiter-Belegung: Schneller Personalüberblick und damit optimierter Ressourceneinsatz. Engpässe und Überhänge werden sofort sichtbar.
-
Job control: Every employee present has assigned jobs based on the available job volume.
-
Standards-based process control: Recurring management tasks are visualised. Compliance with defined standards (e.g. occupational safety, cleanliness and order) is ensured by on-site process controls. These process controls serve on the one hand to prevent errors and on the other hand as a source of possible optimisation measures
-
Key figures: By means of deviations from the target value, weak points can be identified and a problem-solving process can be initiated immediately.
-
Problem-solving process: The modules described above ultimately serve to quickly identify deviations. The structured problem-solving process serves to restore the target state.
-
Diese Board-Termine sind Teil einer abteilungsübergreifenden Kommunikationsstruktur und bilden den Rahmen für strukturierte Tagesabläufe.
Serves to create standards in the workplace, through which faults and deviations can be clearly identified.
(Quelle: TBM Consulting Group http://www.tbmcg.com/de/about/ terminology.php)
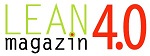
Simultaneous engineering is a method that shortens the time needed to bring new products to market. This time saving is made possible by the fact that employees from different areas of a company are simultaneously involved in the creation of a product, production planning, procurement of resources or marketing strategy. Those involved in the project are grouped into one or more simultaneous engineering groups. Communication channels are reduced in this way and cooperation is strengthened. External companies can also participate in the project in parallel and synchronously using this method.
(Quelle: GPM)
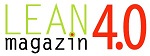
Changeover of a machine in less than 10 minutes: the time between the last good part of a series to the first good part of the next series applies. Synonym: "Single-digit set-up time".
(Quelle: TBM Consulting Group http://www.tbmcg.com/de/about/ terminology.php)
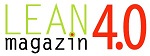
Situation analysis is usually understood to be the thorough, method-supported investigation and evaluation of the status of project work. Such a planning and decision-making situation can arise at the beginning, at the end or even during the project. Based on project progress reports, deviations must be analysed and corrective measures must be checked. In project management, various methods are used for situation analysis.
(Quelle: GPM)
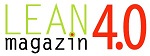
A situation report usually contains global statements on the current situation, deadlines and cost situations, e.g. whether contractually negotiated deadlines can be met or not, whether a certain budget is exceeded, etc. If necessary, the data can be explained by graphic representations. The situation report should inform a specific group of addressees at regular intervals about all relevant project events.
(Quelle: GPM)
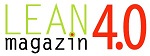
Six Sigma was developed by Motorola in the 1980s as a Total Quality Management approach. It is comparable with Malcolm Baldrige Quality Award of the U.S. or the European Quality Award . However, Six Sigma places more demands on a company and its organisation than the systems mentioned above. The difference is that Malcolm Baldrige Quality Award of the U.S. and European Quality Award provide a framework, but do not describe how a Total Quality Management System can be developed and implemented in detail. The goal of Six Sigma is to rethink the whole company. The core of the Six Sigma approach is the continuous improvement of Total Quality Management and the substantial improvement of business results. It is a benchmark for quality management that strives for perfection. The Six Sigma principle strives for strategies based on quantitative measurement and attempts to optimise processes, limit deviations or scatter and eliminate errors or quality problems of all kinds. For this purpose, established techniques of quality assurance are combined with simple and higher methods of data analysis and systematic training of employees at all levels of an organisation. In order to implement Six Sigma, a structure and a team with defined roles and responsibilities is required in the company.
See also: Total quality management, Quality Management.
(Source: www.quality.de)
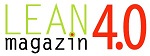
Smart objects are any products that can record, process and exchange information about the location and condition of a product using state-of-the-art technologies such as identification, actuators and sensors. This is intended to close the gap between the physical supply chain and information systems.
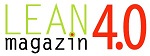
Changeover of a machine in less than 10 minutes: the time between the last good part of a series to the first good part of the next series applies. Synonym: "Single-digit set-up time".
(Quelle: TBM Consulting Group http://www.tbmcg.com/de/about/terminology.php)
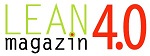
An immediate report must be prepared without request if significant deviations occur in the course of the project. Usually within 24 to 48 hours, the project manager, the management or the client must be informed of the current situation. An immediate report should deal with the problems that have occurred, name the effects on technology, deadlines, costs and capacities and suggest possible countermeasures.
(Quelle: GPM)
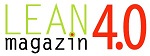
Software configuration management (SCM) is not an independent discipline but a special form of general configuration management and is therefore also subject to its principles. This special form is related to the characteristics of the product software. Here, a more compelling and deeper principle of reference configuration and change management in connection with more intensive reviews and audits is necessary.
(Quelle: GPM)
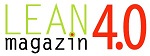
The term social aggregate refers to the direct spatial presence of persons in the loosest form of relationship, a short-term accumulation and fleeting encounter of individuals who have no motivation or possibility to enter into a permanent mutual communication and interaction relationship. This applies, for example, to passengers in a public bus or people in a queue.
(Quelle: Schneider: Lexikon zu Team und Teamarbeit)
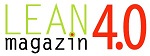
The result of a sociometric test can be illustrated in a sociogram. By means of different symbols, the recorded relationships are shown, taking into account intensity and direction. One differentiates between basic types of social relationships: the isolated element, the dyad, the chain, the star, the pyramid. With an analysis of the sociogram, possible help can be given to normalise the group structure.
(Quelle: Gabler Management, Schneider/Lexikon zu Team und Teamarbeit)
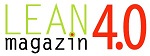
This tabular list of recorded social relationships is another form of presentation of a sociometric test. It is suitable for a precise analysis, but the sociomatrix lacks the clarity of the sociogram.
(Quelle: Gabler Management)
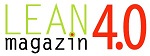
Sociometry is used to represent the informal organisation, i.e. the extent to which the formally defined organisation is implemented in the workplace and the relationships among employees. This is done through observation and questioning. Possible questions of a standardised interview in the context of such a sociometric test could be Who in the group do you like, which person(s) are unlikable With whom do you like to work together, with whom not, etc. In this way, the social structure in the different working groups becomes transparent and possible effects on the Project become apparent
(Quelle: Schneider/Lexikon zu Team und Teamarbeit, Gabler Management)
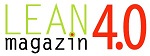
The data obtained from a sociometric test can be used in mathematical formulae. This results in coefficients that allow statements to be made about certain people (e.g. their social status).
(Quelle: Gabler Management)
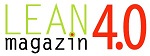
If the end of an activity is linked to the start of its predecessor, in the network technique we speak of the relationship of the jump sequence.
(Quelle: GPM)
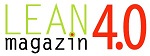
The optimum combination of employees and machines with minimum use of labour, space, inventory and equipment..
(Quelle: TBM Consulting Group http://www.tbmcg.com/de/about/terminology.php)
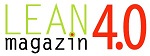
A defined sequence of work steps that an employee must perform within the Cycle time .
(Quelle: TBM Consulting Group http://www.tbmcg.com/de/about/terminology.php)
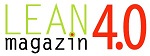
A document that shows the sequence of production steps for an employee. It is used to show the optimum combination of man and machine.
(Quelle: TBM Consulting Group http://www.tbmcg.com/de/about/terminology.php)
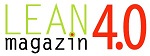
Minimum amount of material needed to complete an employee cycle without delay.
(Quelle: TBM Consulting Group http://www.tbmcg.com/de/about/terminology.php)
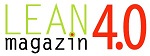
The drawing of a workstation or cell showing how the standard work is to be performed.
(Quelle: TBM Consulting Group http://www.tbmcg.com/de/about/terminology.php)
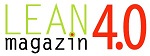
The area of investigation must already be clearly defined and known in a standardised interview. The structure and procedure are strictly defined and bound to a catalogue of questions, which determines the content, formulation and order of the questions. The interviewer reads out the questions one after the other, whereby improvisation by both sides (interviewer/respondent) is not possible, as alternative answers are usually prescribed. The disadvantages are often the high preparation effort, the rigid execution and the compulsion to formulate the questions clearly. On the other hand there is the simple evaluation, the easy comparison of results and the use of several interviewers.
(Quelle: Mehrmann/Wirtz)
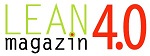
A status report integrates all project parameters in a targeted manner and makes it possible to summarise all information from the lowest to the highest reporting level within a defined period of time (e.g. monthly). It is therefore more detailed than a situation report. The status report should mention under a bullet point the most important current and expected events, problems and trends, the latter even being represented graphically or illustrated by symbols. The status report must explain the situation in terms of essential information about the current reporting period (e.g. results, problems, etc.) and subsequent ones (e.g. objectives, activities, events). The schedule and cost situation must also be described in detail. Depending on the project, the situation of subcontractors, contract negotiations and offers, unfulfilled guarantees and warranties, as well as the market or competitive situation can also be described..
(Quelle: GPM)
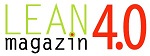
The status meeting takes place regularly at fixed intervals between the project manager and the project officers. Its purpose is to determine the progress of the project, i.e. to observe the extent to which services, time, costs and capacity are being adhered to in terms of planning. In addition, potential problems can be identified and the necessary countermeasures can be discussed.
(Quelle: GPM)
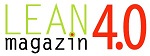
See steering committee
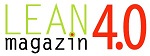
The authorisation of employees to interrupt the process in the event of malfunctions, thus preventing errors or standard deviations from being passed on to downstream processes.
(Quelle: TBM Consulting Group http://www.tbmcg.com/de/about/ terminology.php)
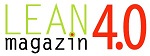
The ability to detect and rectify a fault, i.e. any deviation from a standard operation, in good time.
(Quelle: TBM Consulting Group http://www.tbmcg.com/de/about/ terminology.php)
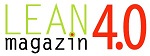
What non-qualifiable benefits does the project bring?
See also: Project goal, Cost targets, Target dates.
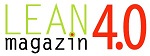
The concept of structure can be viewed from various perspectives - such as philosophical, scientific-technical, mathematical. What they all have in common is that an ordered whole is represented in its structure, in its fabric, and that parts are examined in their contexts and regularities. For example, the structure of materials or the structure of atoms, the spatial structure of which is subject to certain laws, is recalled here.
See also: Structuring.
(Quelle: GPM)
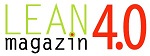
The structured interview incorporates parts of the free and the standardised interview, so that it is possible to deviate from the sequence and formulation of the prescribed list of questions during the interview. However, the interviewer must have a high level of expertise. The survey effort is considerably lower than in a free interview and the answers given can be easily compared.
(Quelle: Mehrmann/Wirtz)
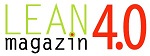
eation of systems of classification of products, processes, resources, costs, etc. The focus is on the Work breakdown structure, which also represents the project delimitation.
(Quelle: GPM)
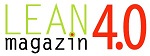
Machines run at full capacity without interruption, regardless of costs and consequences. In general, this leads to a significant increase in the biggest cost item in production: the material.
(Quelle: TBM Consulting Group http://www.tbmcg.com/de/about/ terminology.php)
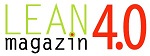
A place along the assembly lines/belt where parts are sorted and prepared for transfer to machine operators.
(Quelle: TBM Consulting Group http://www.tbmcg.com/de/about/ terminology.php)
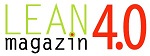
Supervision is a function of controlling, reflecting and securing organisational processes, which can be performed by an individual (supervisor) or a group (supervision team). It includes the psychologically and group-dynamically based counselling of the performers in their task completion and their critical review of their own activity with the aspect of optimising and evaluating the performance of the individual or the group. It is hoped that this will lead to a higher level of qualification and an improved professional competence of the employees.
(Quelle: Schneider: Lexikon zu Team und Teamarbeit)
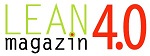
Supplier Managed Inventory, is a logistical tool to improve performance in the supply chain, where the supplier has access to the customer's inventory and demand data.
See also: Vendor Managed Inventory (VMI).
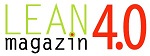
This elaborate method, which seeks to find alternative solutions, is based on the theory of creativity. By means of synectics, the unconsciously occurring creative thought processes are to be stimulated and made conscious. Through the formation of analogies, the actual problem is first of all distracted from the problem itself, in order to later establish a connection between analogy and problem, which leads to new proposals for solutions. This is done in four steps:
-
Dealing with the problem specification
-
Alienation of the subject matter
-
Preparation of compounds
-
Development of solution ideas
Synthesis sessions should be led by a moderator. The number of participants should not exceed twelve. A procedure using this synetic method can take two to three hours, but can also last several days.
(Quelle: GPM, Gabler Management)
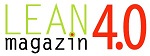
This method of identifying objectives and strategies, which often serves to analyse the risks involved in large-scale projects, is based on systematically designed visions of the future which are based on given situations. From these, future constellations are developed step by step within a certain time frame as a sequence of imaginary events (scenarios). As a graphical representation, the Battelle Institute proposes a funnel that opens up from the present towards the future and summarises all possible bad and favourable developments and events of several scenarios.
(Quelle: Mehrmann/Wirtz, Gabler Management)
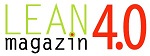
T
Cycle time: The daily working time divided by the number of pieces required by the customer per day.
(Quelle: TBM Consulting Group http://www.tbmcg.com/de/about/ terminology.php)
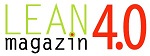
See Ishikawa diagram
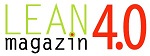
This group of people with different expertise has the task of analysing a specific problem and finding and applying proposed solutions. A task force group often receives a time limit to be observed and forms the subsidiary organisation to a larger group (e.g. a commission). It is entrusted with a sub-problem of the larger group, but its members are not detached from its original organisational structure.
(Quelle: Schneider: Lexikon zu Team und Teamarbeit)
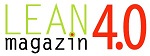
A team differs from a normal group of people in that the individual team members develop a sense of togetherness, accept each other and stand by themselves, the others and their goals.
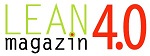
Team development is the (time) phase that a working group needs in order to become an optimal team by improving mutual communication and cooperation.
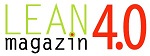
The development of a working group into a real team generally takes place in the following four phases:
The team is put together during the forming phase. By carefully scanning the group, the different characters of the group members crystallize. The subsequent conflict phase (Storming) brings to light different points of view and differences of opinion and thus determines the pecking order. Once the disagreements have been resolved, one speaks of the norming phase (Norming), in which the cohesion of the group is developed and strengthened by defining the common rules of the game. As soon as each group member can carry out his or her work without restriction, the work phase (performing) is reached, which forms the conclusion of the team development. If this sequence of phases is followed and each individual phase is passed through correctly, optimal teamwork is guaranteed.
(Quelle: Kirchner/Pink, Mehrmann/Wirtz, Schneider: Lexikon zu Team und Teamarbeit)
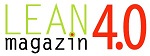
Definition according to DIN: A subtask is a part of projec twhich was published in the Work breakdown structure can be further broken down.
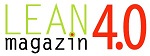
Subnetwork technology is understood to mean the splitting of an overall network plan into several subnetworks which only cover a certain part of the project and are structurally linked to other subnetworks of the same project. It is mainly used for large-scale projects. The subnetwork technique involves the decomposition of the network plan and the composition of the resulting subnetworks, which is called network diagram .In the latter case, care must be taken that different number ranges are used for the operations of the different subnetworks (e.g. for the operations of subnetwork 1 the numbers 11-19, for those of subnetwork 2 the numbers 21-29, for those of subnetwork 3 the numbers 31-39, etc.). A network can be subdivided according to several aspects, e.g. by project phases, by the subtasks listed in the work breakdown structure, by organisational or functional aspects.
(Quelle: GPM)
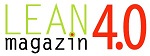
Machines run at full capacity without interruption, regardless of costs and consequences. In general, this leads to a significant increase in the biggest cost item in production: the material.
(Quelle: TBM Consulting Group http://www.tbmcg.com/de/about/ terminology.php)
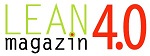
An appointment is a time expressed by calendar date and/or time (definition according to DIN). Appointments as well as times can be given or calculated, they can denote target or actual. An appointment/time can be fixed or not.
(Quelle: GPM)
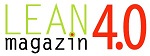
See process management
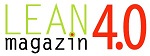
See time management
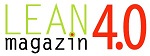
he Theory of Constraints (ToC) is based on ideas by Eliyahu M. Goldratt and deals with the question of how to maximise the throughput of a system. The basic insight of the approach is that every system has exactly one bottleneck, which, similar to the narrowest point in a pipe system, limits the throughput, no matter how much you put into the system at the front end. The system is optimised as follows:
-
IIdentify the bottleneck. There are never two bottlenecks unless we are dealing with completely independent systems or value streams. But we look at each system individually.
-
Use the bottleneck optimally. This is almost never the case before. Often attempts are made to increase local efficiencies at all possible points in the system. However, this only leads to an improvement in the overall system if it happens at the bottleneck. All other improvements are irrelevant for the total throughput!
-
Align the management with the bottleneck, i.e. subordinate all activities to it. All positions in the system or in the company or project should work in such a way that the bottleneck - this can be a machine or a person or a team - is used to full capacity, has no idle time and can concentrate on one main task. Everything else is a waste!
-
Extend the bottleneck. Only when the bottleneck is used optimally and the throughput of the system is still not high enough, we expand it, e.g. by purchasing another machine or by increasing the number of staff in the bottleneck team.
-
If the bottleneck is extended or fully utilised, there is often a shift, because the entire system now has a bottleneck again. This can be the same or - what is more likely - a new one.
One project management method based on the bottleneck theory is the so-called Critical Chain Project Management.
(Quelle: Alexander Kriegisch, Scrum-Master.de Siehe auch: Wikipedia - Theory of Constraints ToC4U - Artikelserie über die ToC)
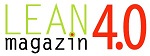
The speed at which the entire system generates money.
(Quelle: TBM Consulting Group http://www.tbmcg.com/de/about/ terminology.php)
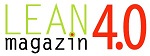
Strategy in which corporate goals and time-saving principles interact.
(Quelle: TBM Consulting Group http://www.tbmcg.com/de/about/ terminology.php)
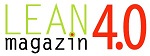
TOP-Mapping is a survey method developed by the computer manufacturer Digital Equipment, which tries to represent the communication flow of a company by means of a few symbols (e.g. islands, bridges, roads, etc.). TOP-Maps, which resemble topological maps, can be used to illustrate the functioning of an entire company, a division, a department or an individual work group. This allows managers to create cross-functional representations of their business and information flows. Once the TOP map has been created by the managers, a transparent foil is placed over it. Four new symbols make it possible to identify an information solution, as well as discuss alternative solutions and a possible plan to purchase computer-integrated systems that adapt to the respective company structure. After a TOP-mapping, one thus receives two maps: the first could be called a visualised as-is analysis, the second a target concept.
(Quelle: Mehrmann/Wirtz)
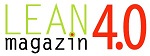
Total Productive Maintenance (TPM) is a modern maintenance concept that optimises the performance of the entire plant management by integrating production and maintenance. Today TPM is also interpreted as Total Productive Manufacturing or Total Productive Management in the sense of a comprehensive production system. Parallels to Kaizen or Lean production can be seen here. From the basic idea, TPM is a programme for continuous improvement in all areas of a company. It is primarily about chasing losses and waste with the aim of zero defects, zero failures, zero quality losses, zero accidents, etc. The main focus is in the area of production. The eight pillars of TPM:
-
Continuous improvement: Application-related elimination of the 6 loss types.
-
Autonomous maintenance: The plant operator should carry out inspection, cleaning and lubrication work in the first, and in further steps also minor maintenance work independently.
-
Planned maintenance: Ensuring 100% availability of the plants and reporting KAIZEN actions by the maintenance department.
-
Training and education: To qualify employees according to requirements to improve operating and maintenance qualifications.
-
Start-up monitoring: To realise an almost vertical start-up curve for new products and plants.
-
Quality management: Realisation of the zero quality defect target for products and plants.
-
TPM in administrative areas: Eliminate losses and waste in departments that do not directly produce.
-
Occupational safety, environmental and health protection: implementing the zero accident requirement in the company.
Total Productive Management has as its basic idea the elimination of waste in all areas of a company. 6 types of losses:
-
Losses due to plant failures (machine downtime)
-
Set-up and set-up losses
-
Losses due to idling and short downtimes
-
losses due to reduced cycle or operating speed
-
losses due to start-up difficulties
-
Loss of quality (scrap, rework)
(Quelle: Wikipedia)
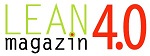
TQM is an approach to quality managementdeveloped by Dr. Joseph Juran, which is aimed at putting the company in a leading position vis-à-vis its competitors with six success factors simultaneously. The following methods are included in TQM:
- Zero-error principle (in every processing stage)
- The principle of 5 Why Kaizen as a systematic learning process in the workplace
- Simultaneous engineering; i.e. networking, feedback, cross-functional teams, the process idea.
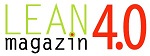
Lehnt an einige der frühen Prinzipien von Henry Ford an und beschreibt die Geschäftsphilosophie eines der erfolgreichsten Unternehmen der Welt. TPS baut auf der Produktionsnivellierung auf und arbeitet außerdem mit Just-In-Time und Jidoka.
(Quelle: TBM Consulting Group http://www.tbmcg.com/de/about/ terminology.php)
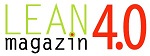
Hoshin-Kanri Hoshin-Kanri (from the Japanese: compass needle management or planning) contains a target hierarchy. The multi-annual goal (Ideal or Vision) is the North Star (True North), which is the basis for the annual goals, but also for the concrete improvement activities. Because the North Star is oriented towards customer needs, the previously different and sometimes contradictory management objectives can be redefined, synchronised and coordinated. This resolves some of the previous conflicting objectives.
(Quelle: Wikipedia)
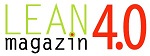
U
Holdings which accumulate between the different work steps.
(Quelle: TBM Consulting Group http://www.tbmcg.com/de/about/ terminology.php)
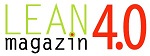
The implementation plan should clarify the milestones and actions of a projec t In doing so, the logical and temporal dependencies of the network technique are disregarded and limited to a detailed planning presentation of the procedure. With the division into columns and the concise formulations, the implementation planning offers an optimal overview of the upcoming activities and possible problems. In the column Topic/Action the planning object is first of all explained in more detail. Then the objective of the activity is presented, followed by the "Path" column, which explains the procedure and the further steps. The next column determines who is responsible for implementation. Under budget one deals with the amount of (time) expenditure. If necessary, milestones and memoranda (actions not yet firmly planned) can be listed on the first page of an implementation plan. Implementation plans must be revised and updated at regular intervals so that they can be used to compare the planned and actual course of the project. It is also advantageous to review and discuss the implementation planning several times in a team.
(Quelle: Gabler Management)
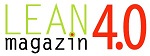
Definition according to DIN: The independent buffer time is the period of time by which an event or process can be postponed if its previous events or predecessors are in the latest position and its subsequent events or successors are in the earliest position.
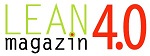
See Ishikawa diagram
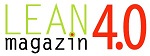
V
Any activity that processes a product or service in accordance with customer requirements.
(Quelle: TBM Consulting Group http://www.tbmcg.com/de/about/ terminology.php)
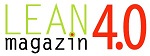
Calculation of total lead time and value-added time to determine the percentage of value-added activities.
(Quelle: TBM Consulting Group http://www.tbmcg.com/de/about/ terminology.php)
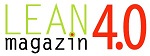
A drawing that illustrates the flow of materials and information from the supplier through production to the customer. It also includes calculations of total cycle time and value added time.
(Quelle: TBM Consulting Group http://www.tbmcg.com/de/about/ terminology.php)
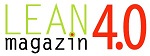
A drawing that illustrates the flow of materials and information from the supplier through production to the customer. It also includes calculations of total cycle time and value added time.
(Quelle: TBM Consulting Group http://www.tbmcg.com/de/about/ terminology.php)
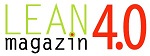
Value Stream Management documents, in addition to the daily management of the areas of an organisation along the value stream, the complete change process starting with the identification and recording of a value stream (actual state, current state map) up to the planned transfer to a target state (future state map, FSM). Value Stream Mapping is a simplified graphical representation of complex operational processes to identify waste and main improvement potentials from an overall view. Successfully applied, Value Stream Mapping is an instrument for the holistic improvement of the production flow, resulting in cost reduced production. In addition, individual customer requirements can be processed more flexibly.
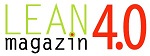
Vendor Managed Inventory (VMI) also known as Inventory or Supplier Managed Inventoryis a logistical tool for improving supply chain performance, where the supplier has access to the customer's inventory and demand data. How did VMI work?
-
The customer's warehouse is monitored by the supplier
-
Filling and management of the warehouse is the responsibility of the supplier
-
The supplier monitors the customer's stock
-
The customer provides the supplier with further information
-
The best possible replenishment quantity (as small as possible but as large as necessary) and also the time are determined by the supplier.
Since planning and scheduling tasks are eliminated and the material does not become the customer's property until it is removed from the warehouse, VMI offers the customer great advantages.
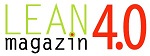
The interlacing number standardised in DIN 69900 Part 1 is a key figure in planning technology. It reflects the interdependence within a network, which can be calculated with the following formula:
V = P/(K - 1)
The size P stands for the number of arrows in the network, K indicates the number of nodes. The higher the value of the interlacing number, the more difficult it is to display and maintain the network.
(Quelle: GPM)
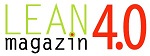
The selling costs result from the Overhead costs and the sum of the Production costs.
(Source: Madauss: Projektmanagement)
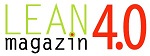
Any activity that consumes resources without directly contributing to the added value of the product.
(Quelle: TBM Consulting Group http://www.tbmcg.com/de/about/ terminology.php)
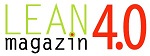
One speaks of a vertical team when the cooperation between supervisor and employee runs smoothly and in a harmonious relationship.
(Quelle: Schneider: Lexikon zu Team und Teamarbeit)
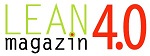
Drafting, analysis, conclusion and amendment of contracts, taking into account the connections to change and claim management and monitoring of contract performance.
(Quelle: GPM)
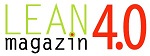
Virtual Project Management Office refers to a team or project room. They are more than project management tools and are also often available as rental software. They serve as an information and communication portal for all participating project members, which is accessible worldwide via the Internet. The scope of functions usually consists of features for project planning, control and monitoring, e-mail, calendar, chat, shared file storage but rarely includes special features as with e-collaboration software.
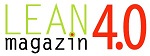
Serves to create standards in the workplace, through which faults and deviations can be clearly identified.
(Quelle: TBM Consulting Group http://www.tbmcg.com/de/about/ terminology.php)
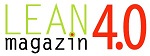
System that allows all employees to immediately detect faults in the workplace, no matter how familiar they are with the process.
(Quelle: TBM Consulting Group http://www.tbmcg.com/de/about/ terminology.php)
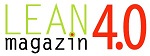
An event is a sequence element that describes a specific event. This also includes that the beginning and end are defined (definition according to DIN 69900). In practice, the synonyms work cycle, activity, job or activity are sometimes used.
(Quelle: GPM)
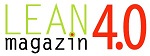
The activity node is an elementary part of the network. Each node within the network represents a single activity. It is represented graphically as a rectangle and initially contains the activity name and number under which an activity is listed in the activity list. Below the activity number the duration of the activity (D) is noted, below the activity name the total float time (GP) and the free float time (FP). Outside the rectangle, the earliest start time (FAZ) and the latest start time (SAZ) are noted on the left-hand edge, which marks the start of the operation. The FAZ is noted above the node, the SAZ below the node. Parallel to this, the earliest finish time (FEZ) and latest finish time (SEZ) are noted on the right-hand side, which symbolises the end of the operation. The time dependencies between the operations are shown by arrows.
(Quelle: Mehrmann/Wirtz)
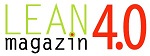
Definition according to DIN: The VKN is a network plan based on a procedure in which mainly activities are described and represented by arrows.
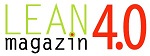
The operation list contains all the operations listed in the work breakdown structure and assigns them a number. You must also specify a predecessor for each activity, that is, which previous activity is the prerequisite for starting the respective activity. The activity list forms the basis of every network.
(Quelle: Mehrmann/Wirtz)
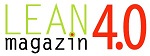
Definition according to DIN: The VON is a network diagram,which is exclusively characterised by the description of activities (independent of the presentation form)
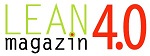
The Project Information, Planning and Control System (VIPSS) is a database-supported, dialogue-oriented project planning and control procedure designed for the central mainframe computer and developed by the Post Office and Dornier GmbH. It is suitable for projects which have a high proportion of creative and difficult-to-plan activities, consist of iterative work steps, involve a large proportion of decentralised forces and employ many creative staff with as much division of labour as possible on site, i.e. for projects which involve an enormous amount of data processing. With the centralised procedure, all projects are registered and protected in a central database so that they can be retrieved by management at any time. This requires an administration that maintains all master data (e.g. cost rates, departments, etc.) and planning models and issues authorisations. Data that has no relation to the project (holiday, illness etc.) is not recorded. VIPSS is also able to adapt models individually to companies and areas of responsibility online.
(Quelle: Mehrmann/ Wirtz)
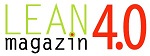
In addition to the daily management of the areas of an organisation along the value stream, value stream management documents the complete change process, starting with the identification and recording of a value stream (actual state - current state map) through to the planned transfer to a target state (future state map, FSM). Value Stream Mapping is a simplified graphical representation of complex operational processes to identify waste and main improvement potentials from an overall view. Successfully applied, Value Stream Mapping is an instrument for the holistic improvement of the production flow and thus results in cost reduced production. In addition, individual customer requirements can be processed more flexibly.
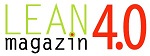
W
The value analysis procedure is intended to improve the revenue-cost ratio by systematically applying known and proven techniques for determining functional structures. The aim is to develop products, production factors, processes and organisations to the highest possible level of economic efficiency. A distinction is made between the value analysis of existing objects (value analysis), which aims to reduce costs, and the value analysis of objects in the development stage (value engineering), which is intended to contribute to cost prevention. The value analysis is characterised by a targeted investigation of the functions of the object under consideration and a division into main and secondary functions. Likewise, a schematic planning process by means of a work planning is necessary, which is to evoke the decision making process by means of a given phase scheme. A further characteristic of value analysis is the temporary, cooperative teamwork of experts from different areas of the company. Heuristic methods of creativity promotion (e.g. brainwriting) and for alternative evaluation (utility value analysis) are essential elements of value analysis. Originally developed for technical objects, it can also be applied to activities, work processes, etc. In project management, value analysis can be used, for example, in product innovation projects to present the product in its functions, to show alternative functional solutions, etc.
(Quelle: GPM)
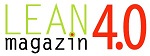
Any activity that processes a product or service in accordance with customer requirements.
(Quelle: TBM Consulting Group http://www.tbmcg.com/de/about/ terminology.php)
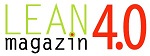
A drawing that illustrates the flow of materials and information from the supplier through production to the customer. It also includes calculations of total cycle time and value added time.
(Quelle: TBM Consulting Group http://www.tbmcg.com/de/about/ terminology.php)
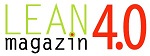
In addition to the daily management of the areas of an organisation along the value stream, the value stream management documents the complete change process, starting with the identification and recording of a value stream (actual state, current state map) through to the planned transfer to a target state (future state map, FSM). Value Stream Mapping is a simplified graphical representation of complex operational processes to identify waste and main improvement potentials from an overall view. Successfully applied, Value Stream Mapping is an instrument for the holistic improvement of the production flow and thus results in cost reduced production. In addition, individual customer requirements can be processed more flexibly.
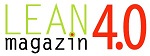
This method of joint decision-making is based on the mathematical formula of Pythagoras:
a²+b²=c²
The opinion (a) of one person does not suppress the opinion (b) of his interlocutor, but both possibilities are transformed into an ideal solution (c) by combining them.
(Quelle: Kirchner/Pink)
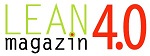
If a working group has successfully completed all team development phases so that each individual member performs at his or her best in the workplace with the utmost motivation and concentration, we speak of a winning team. Any sense of achievement is thus a joint achievement of the entire team.
(Quelle: Kirchner/Pink)
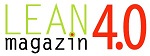
Woods meetings take place outside the usual office atmosphere in a pleasant environment where participants cannot be disturbed by telephone calls etc. Such a meeting may be necessary, for example, if the project has stalled, if employees are emotionally upset, etc. Woods meetings are usually held in conference hotels and are extremely cost-intensive, therefore require meticulous organisation. If you want to use the meeting to resolve internal conflicts, you should engage an external facilitator. Likewise, the hierarchy should be left out of all meetings. In consultation with the participants, documentation of the meeting can also be useful.
(Quelle: Mehrmann/Wirtz)
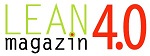
The correct work steps of an employee, executed in the correct order.
(Quelle: TBM Consulting Group http://www.tbmcg.com/de/about/ terminology.php)
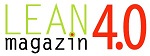
Holdings which accumulate between the different work steps.
(Quelle: TBM Consulting Group http://www.tbmcg.com/de/about/ terminology.php)
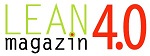
The term workflow describes the systematically designed workflow in business processes. This technical term stands for the entirety of processing and transporting documents, which are the subject of business processes. Likewise, the term workflow takes into account the automation of the control of data transport from person to person, whereby the documents are passed on from processor to processor and the documents are supplemented by individual data. The automatic linking of different applications, as well as the reuse and joint use of the data are important synergy effects. With workflows, idle times, duplication of work, media breaks and other sources of loss can be avoided.
(Quelle: GPM)
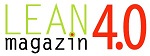
All relevant work processes of a division are coordinated and controlled. If, for example, a salesperson takes an order, the customer data runs into the workflow. The warehouse stock is queried, missing parts are reordered from the supplier, the delivery is made ready for dispatch, invoicing is initiated and the order is passed on to financial accounting. Workflow management systems promise cost reductions and improved customer orientation through the cross-departmental reorganisation of business processes.
(Quelle: Report Wissensmanagement: Wie deutsche Firmen ihr Wissen profitabel machen. Herausgeber: Prof. Dr. C.H. Antoni, Dr. Ing. T. Sommerlatte)
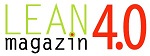
lanning systems that help to coordinate resources and capacities. Such as scheduling systems: All participants in a project enter their deadlines. If a common time for a meeting is sought, corresponding search functions find the place where everyone is available.
(Quelle: Report Wissensmanagement: Wie deutsche Firmen ihr Wissen profitabel machen. Herausgeber: Prof. Dr. C.H. Antoni, Dr. Ing. T. Sommerlatte)
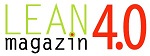
Z
is method of estimating the effort required is used to determine the work progress of a work package. The criterion of dependency is the time elapsed since the start of work. An example: A Work package is set at six months. After three months, the progress of the work is 50% of its value.
(Quelle: Mehrmann/Wirtz)
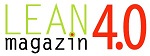
Deadline planning: Evaluation of operations in time units (durations) Deadline planning and controlling: Consideration of time as a limited resource (calendar, working time regulation, fixed deadlines).
(Quelle: GPM)
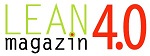
See time share method
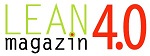
The point in time is a fixed point in the sequence, the position of which is described by time units (e.g. minutes, days, weeks) and is related to a zero point (definition according to DIN). The points in time in the context of a project time analysis always concern the occurrence of an event (especially the start and end event of processes, work packages, subtasks, etc.). The start of a project is usually chosen as the zero point.
(Quelle: GPM)
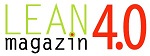
Strategy in which corporate goals and time-saving principles interact.
(Quelle: TBM Consulting Group http://www.tbmcg.com/de/about/ terminology.php)
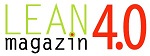
Arrangement of the machines according to the actual process sequence. The machine workers stay in the cell and the material is handed to them from outside the cell.
(Quelle: TBM Consulting Group http://www.tbmcg.com/de/about/ terminology.php)
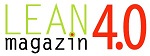
Identification of all interests and objectives relevant to the project, their evaluation and translation into operational objectives, and finally their definition and monitoring
(Quelle: GPM)
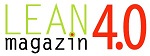
Means the target group-specific handling of analysed and segmented customers, the focus is on the segment-specific development of marketing campaigns.
(Quelle: Reinhold Rapp: Customer Relationship Management Campus 2000)
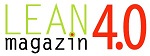
A random experiment is a process that can be repeated as often as desired and whose event and result remain undetermined, e.g. coin toss, dice etc.
(Quelle: GPM)
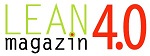
The time required by a machine operator to complete a job. Usually the time until the cycle starts again from the beginning.
See Employee cycle time, Machine cycle time.
(Quelle: TBM Consulting Group http://www.tbmcg.com/de/about/ terminology.php)
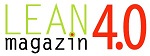